When you put off maintenance, your equipment starts breaking down bit by bit. Your machines become less efficient, use more energy, and are more likely to fail.
Let’s be realistic though — every organization has to postpone some maintenance. Even the best-run facilities face limits on time, people, and money. The goal isn’t to fix everything immediately, that’s just not practical.
Instead, you need to be smart about what you postpone — and have a deferred maintenance plan that will get you back on track if your backlog starts getting out of control.
Let’s arm you with the knowledge to do just that.
What is deferred maintenance?
Deferred maintenance refers to the practice of postponing asset repair or upkeep due to financial constraints, lack of resources, or strategic prioritization.
Deferred maintenance can be:
- Intentional: You deliberately delay maintenance work to focus on a higher-priority project, prioritize short-term operational output to meet demand, or other strategic reasons.
- Forced: You postpone maintenance work because of a lack of resources — be it time, money, parts, or labor.
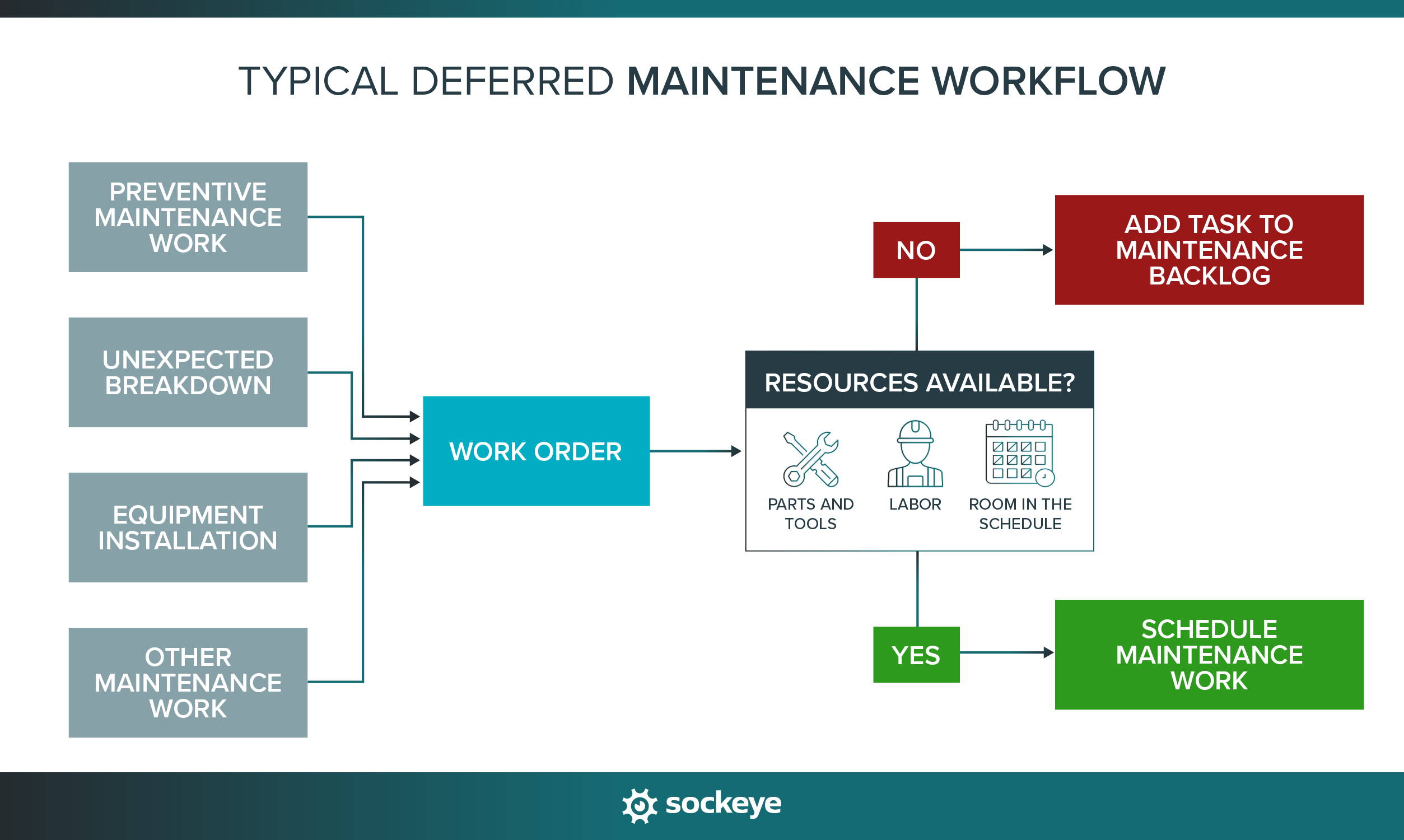
Deferred maintenance examples
Here are some examples that show how maintenance work can be strategically postponed when there are valid operational or business reasons:
- Seasonal production demands: Take a factory that makes holiday decorations. During their busy season, they might postpone non-urgent repairs to keep production moving.
- Resource optimization: Think about a plant with three machines all needing the same repair specialist. Instead of scheduling three costly separate visits, they’ll plan all the work for a single week. Smart scheduling saves both time and money while getting all the repairs done properly.
- Planned equipment upgrades: Picture a company that’s upgrading its packaging line in three months. The current line needs new belts, but it should run safely until the replacement arrives. They decide to save those maintenance dollars for the upcoming upgrade, while keeping a close eye on the existing equipment.
Despite these valid reasons, the reality is that maintenance planners and schedulers often face forced deferrals due to resource constraints.
Usually, scheduled work must be deferred because of more pressing reactive work. For example, the two technicians supposed to perform the scheduled preventive maintenance on the automated material handling system had to race to handle the emergency repair on a CNC machine instead because its coolant filtration system began to overflow.
Common causes of deferred maintenance
Budget constraints and poor organization are the two foundational issues behind most maintenance delays.
These two problems feed into each other. With limited funds, you end up fixing things only when they break instead of preventing problems. And when your team isn’t well organized, you waste the limited resources you do have — and your maintenance backlog continues to grow.
Common causes of deferred maintenance include:
- Lack of personnel: Insufficient staffing forces teams to prioritize urgent issues, leaving routine maintenance tasks delayed and backlogged.
- Lack of skill: The scarcity of skilled technicians leads to delays in complex tasks, compounding the backlog as available staff focus on immediate needs.
- Unavailability of tools and parts: Poor inventory management and inadequate forecasting result in delays when essential tools or spare parts are not readily available.
- Poor maintenance planning and scheduling: A lack of clear priorities and coordination causes teams to defer tasks, even when resources are available, leading to disorganized workflows and inefficiencies.
- Too much reactive work: Emergency repairs dominate time and resources, sidelining preventive maintenance and triggering a cycle of recurring breakdowns.
If your backlog is already getting out of control, one way to combat it is with a smart deferred maintenance plan.
Steps for creating a deferred maintenance plan
A deferred maintenance plan provides a systematic framework to address maintenance backlogs while implementing clear guidelines for work delays. It establishes processes that help organizations manage deferred maintenance effectively and safely.
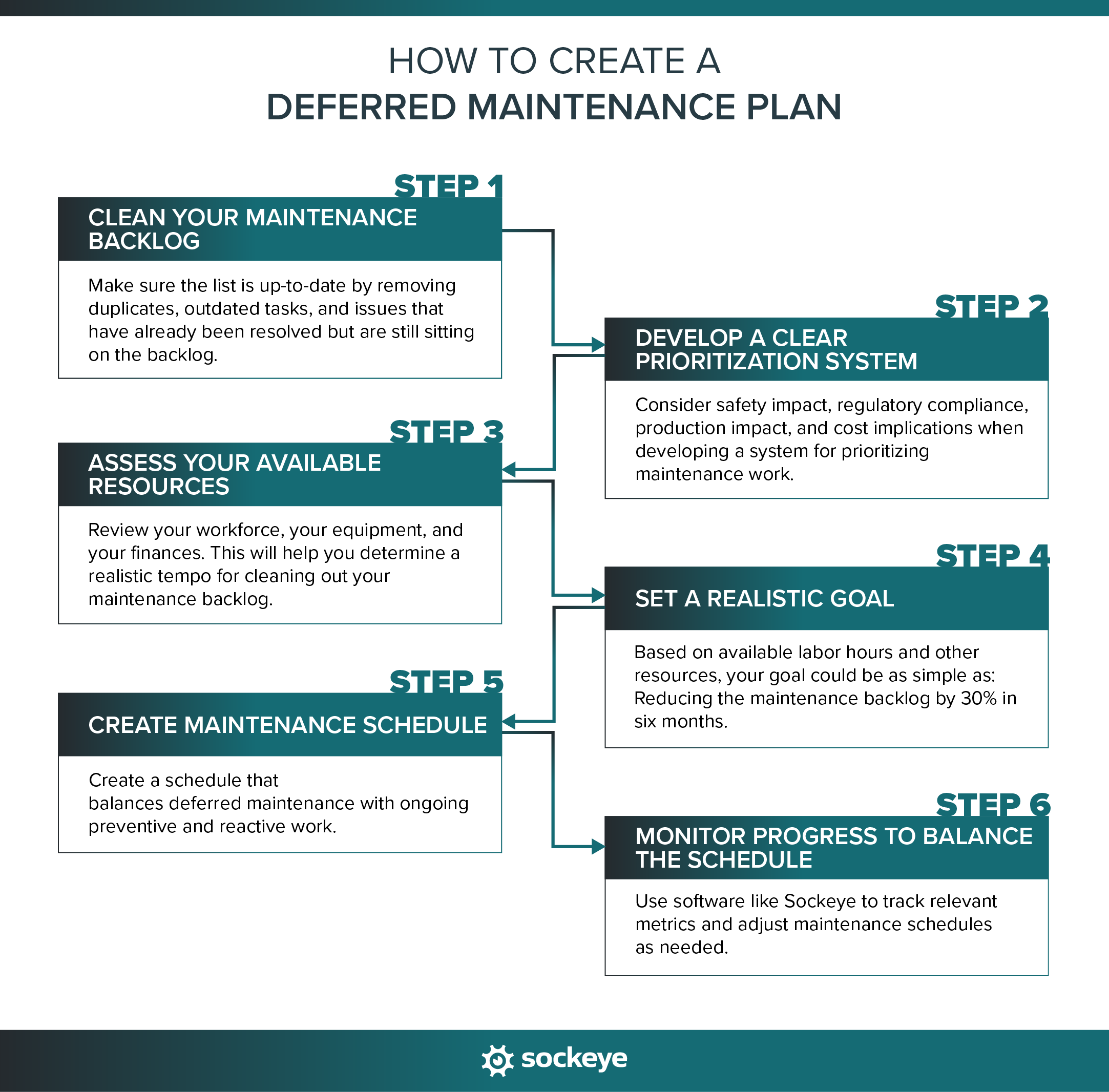
Step #1: Make sure your backlog is clean and up-to-date
Your maintenance backlog should provide a comprehensive overview of all deferred tasks in your facility. Ideally, for each deferred item, you would have:
- Equipment location and tag number
- Task/problem description
- Estimated labor hours and skill requirements (e.g. you need an electrician)
- Required parts and tools to execute work
- Priority level
- Deferral reason
The scope of work for creating such a backlog varies dramatically across facilities. In a well-organized plant, it might simply involve consolidating existing maintenance records from your CMMS and validating their accuracy. Be sure to remove duplicates, outdated tasks, and issues that have already been resolved but are still sitting on the backlog.
For example, Sockeye can provide you with a list of deferred tasks for each piece of equipment, which you can export or use to prioritize and schedule future work.
Other manufacturing facilities might require a complete equipment audit. This means walking through each production area to document equipment conditions and identify maintenance needs.
Step #2: Develop a clear prioritization system for maintenance work
Your prioritization system must reflect a deep understanding of how your operations connect and depend on each other.
For example, has the introduction of new product lines or equipment changed the criticality of certain assets? Has your facility’s safety or quality requirements evolved? These changes might necessitate updates to your prioritization criteria.
When you develop a new (or update existing) prioritization system, consider the following:
- Safety impact: Maintenance tasks that could affect worker safety need immediate attention.
- Regulatory compliance requirements: Industries like food processing or pharmaceutical manufacturing have very specific rules you need to follow.
- Production impact: A failed bearing on your main production line has different implications than the same issue on a backup system.
- Cost implications: How likely is it that postponing this $500 gearbox oil change will result in a $50,000 replacement?
The prioritization system’s real value shows in creating consistency across shifts and departments. Maintenance planners or supervisors make similar decisions when priorities compete, reducing confusion and ensuring critical maintenance receives proper attention.
Step #3: Assess your available resources
Assessing your maintenance resources requires a detailed look at three key areas: your workforce, your equipment, and your finances. This will help you determine a realistic tempo for cleaning out your maintenance backlog.
Start by analyzing your maintenance team’s capacity:
- How many technicians do you have?
- What are their skill levels?
- How many labor hours are typically available after accounting for emergency repairs and routine maintenance?
For instance, if you have 10 technicians working 40-hour weeks, but historically 90% of their time goes to emergency repairs and preventive maintenance, you realistically only have 40 hours per week to address deferred work.
Don’t forget to examine your maintenance tools, parts, and equipment. Do you have the specialized tools and parts needed for your backlogged tasks? Missing equipment can delay work just as much as missing personnel.
Step #4: Set a realistic goal
Setting a goal for your deferred maintenance plan (and tracking KPIs) works much like setting production targets — it creates clear direction and lets you measure progress. Your goal must balance three critical elements:
- How much maintenance have you delayed?
- Which tasks are the most urgent?
- What resources can you actually commit to the deferred work?
Based on available labor hours and other resources, your goal could be as simple as this:
“Reduce maintenance backlog by 30% in six months.”
And based on that goal, it should be fairly straightforward to calculate the volume of work you need to complete each month to make that happen.
Sidenote: Some maintenance work takes much longer to complete than others. To account for this, you can assign a time value to each task and then say that you want to clear 200 hours of maintenance work out of your backlog in six months.
Step #5: Create a maintenance schedule
The prioritization system we discussed earlier can act as your guide, showing you which jobs need to happen first.The real challenge lies in balancing deferred maintenance with ongoing work.
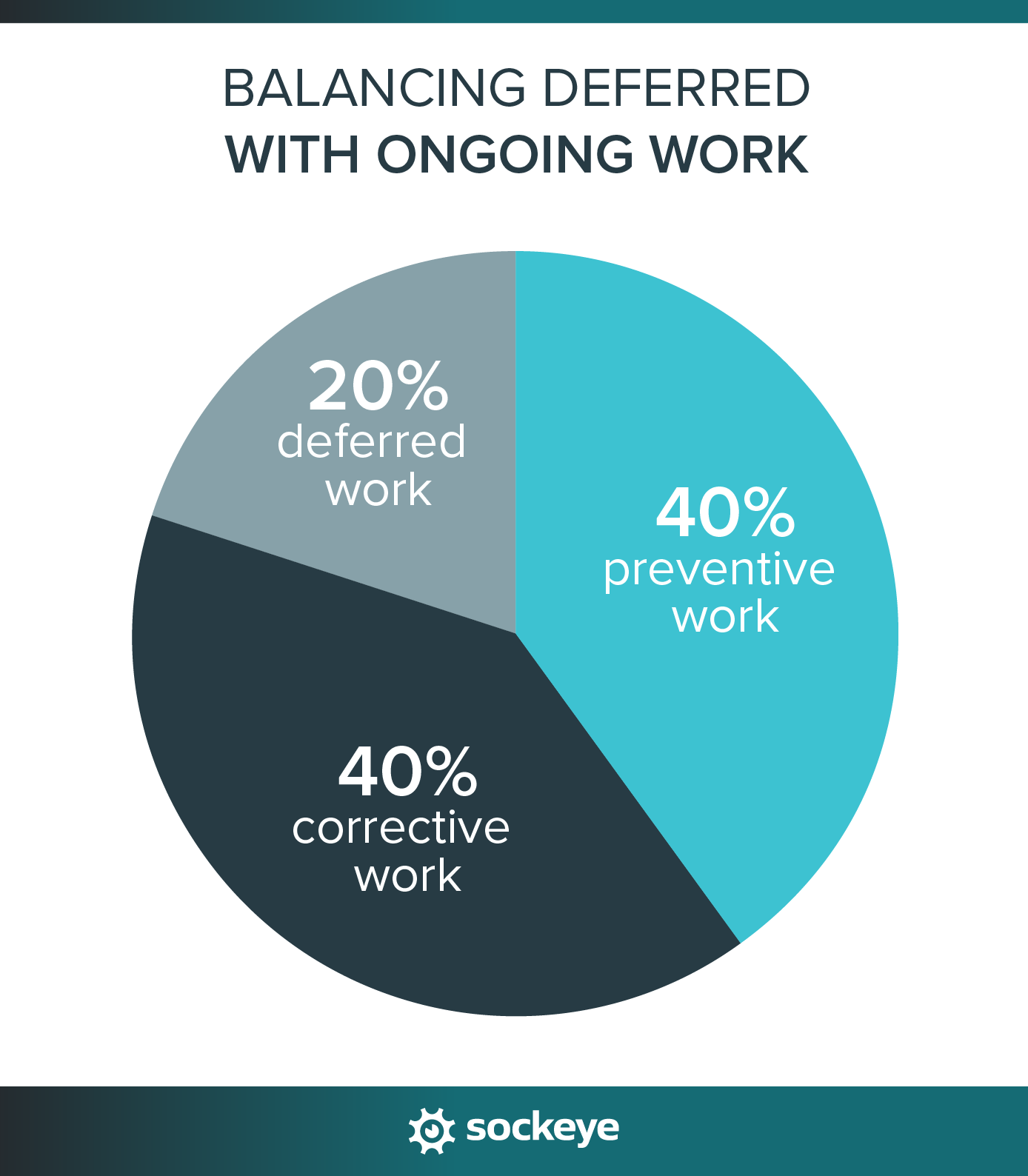
Think of your maintenance capacity as a pie chart where one portion needs to remain dedicated to preventive maintenance to prevent creating new deferred work, another handles corrective maintenance, and the remaining portion tackles your deferred maintenance backlog.
This is where work order scheduling software becomes invaluable. Tools like Sockeye can help you automate parts of your scheduling workflow based on available technician hours, as well as display a visual breakdown of the currently scheduled work (corrective, preventive…).
Instead of manually juggling spreadsheets and trying to remember which technicians are qualified for which tasks, the software helps you quickly create optimized schedules that maximize your team’s efficiency.
Step #6: Monitor progress to balance the schedule
Using a CMMS and Sockeye together provides powerful insights into key performance indicators. You can track metrics like:
- The percentage of delayed work you’re completing
- How long tasks have been waiting
- Time spent on planned work vs emergency fixes
- Available technician hours used
- And much more.
Where Sockeye really shines is in helping you adapt when things don’t go according to plan. You can quickly reshuffle your maintenance schedule while keeping your big-picture goals in mind.
Bonus step: Start addressing the causes of deferred maintenance
Maintenance and reliability managers should work together to identify systemic issues that contribute to maintenance deferrals beyond budget constraints. This might reveal problems like inefficient work processes, inadequate training programs, or poor communication between departments.
The less work you have, the easier it’s going to be to clear out the backlog.
If budget limitations drive most of your maintenance delays, you’ll need to build a strong case for additional resources — and show upper management exactly what deferred maintenance costs the company in the long run.
Stay on track with Sockeye
Using Sockeye’s intelligent scheduling capabilities, your maintenance team can start prioritizing work more efficiently and minimize deferred maintenance.
Need help managing deferred maintenance? Schedule a personalized demo and see how Sockeye can help your team tackle that maintenance backlog while building a more efficient operation for the future.