About Cargill Incorporated
Cargill Incorporated provides food, agriculture, financial, and industrial products and services to the world. Headquartered in Wichita, Kansas, the Cargill Protein Group includes all of Cargill’s North American beef, turkey, food service, food distribution, pet treat, and egg product businesses. With a commitment to supporting the places where they live and work, this Wichita-based division employs more than 32,000 people across the U.S. and Canada at dozens of facilities and offices.
Challenge
Migrating to SAP Left a Gap in Maintenance Scheduling
In 2015, Cade Schoonover, Assistant Vice President of Maintenance and Reliability at Cargill, sought to redeploy work management processes, working closely with dozens of facilities to improve maintenance and reliability processes. At the time, the company migrated their CMMS system to SAP.
“With this migration, we were without a maintenance scheduling solution,” said Cade Schoonover, as he faced either upgrading in-house customized spreadsheets or deploying commercial software. “We had created a scheduling tool using spreadsheets for our previous CMMS. With the transition to SAP, we were losing that functionality.”
Cargill needed a solution that would continue to meet their unique needs. “The work that we do during production, or during sanitation, or the work that we do on weekends is not necessarily the same type of work,” explained Cade Schoonover. “Our customized tool had helped us align our resources with the time available for each type of work required. Even if our spreadsheet tool had worked with SAP, there was still the issue that it was an enormous amount of work just to maintain it.”
In seeking a commercial maintenance scheduling solution, simplicity was critical explained Rick Baldridge, Corporate Reliability Excellence Process Leader, “What I look for is a tool that can enable our business processes without overwhelming people because it’s too cumbersome and complicated. It’s all about simplicity. The simpler it enables the business process, the better. That’s important.”
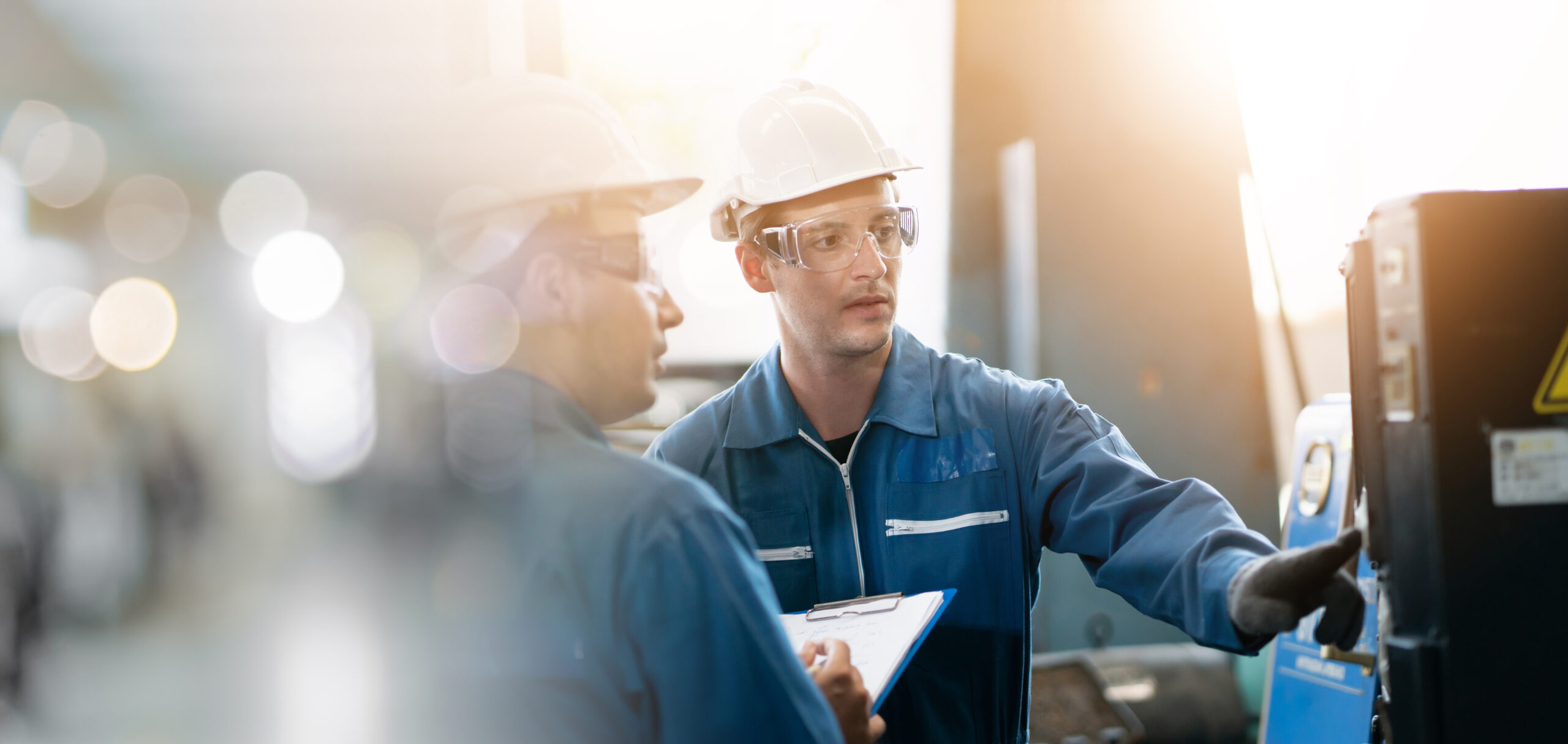
Solution
Sockeye Fits Maintenance Scheduling Process at Cargill Perfectly
After evaluating commercial solutions, the Cargill team chose Sockeye. Sockeye is a SaaS solution that streamlines daily and weekly work order maintenance scheduling for large, physical asset-intensive organizations like Cargill. Simple to use, and with exceptional out-of-the-box fit and function, Sockeye drives effective weekly maintenance scheduling to support optimal reliability and uptime.
“We looked at a lot of different options. They were not doing scheduling like we schedule at Cargill. To customize these solutions would have cost huge programming dollars. The costs were just prohibitive. Quotes received were in the millions of dollars to implement … versus Sockeye which was literally just four figures for all of our 35 facilities,” explained Cade Schoonover, “Sockeye supports our own scheduling process perfectly. It shows the available work. It shows the available labor. It’s just a matter of clicking and dropping. It’s fantastic.”
“It shows the available work. It shows the available labor. It’s just a matter of clicking and dropping. It’s fantastic.”
CADE, ASSISTANT VICE PRESIDENT OF MAINTENANCE AND RELIABILITY
“There are so many ‘scheduling’ tools out there that aren’t really scheduling tools,” added Rick Baldridge. “They’re either dispatch tools or coordination tools. That’s because most people don’t really understand the scheduling business process. It’s clear to me that Sockeye understands scheduling. Right out of the box, Sockeye was great match for our business process. We knew it was a perfect fit.”
When the Cargill Manufacturing Information Technology (MIT) department requested a requirements list to formally evaluate scheduling tool options as part of the purchasing process, Rick boldly replied, “All you need to do is to look at Sockeye, exactly how it schedules maintenance work, that fits our requirements.”
Sockeye is Vendor of the Year
Responsible for spearheading the deployment and adoption of SAP and Sockeye across 35 businesses, Mike Williams, Maintenance Information and Process Lead at the Cargill Protein Group, describe the ease of working with the deployment team at Sockeye, “They have been very accommodating to our needs. If we could give a vendor of the year award, we’d give it to Sockeye! Anything we ask, this team does its best to accommodate us and quickly.”
Sockeye’s Ease of Use and Simplicity Drives User Adoption
“The technical conversion was a piece of cake. Steadfast users of the spreadsheet tool found the transition very seamless,” said Cade Schoonover. “We didn’t have to teach anybody how to do anything differently. Sockeye enabled the processes that already existed within our plants. It’s easy to use. It’s very intuitive. People picked it up very quickly. They’ve taken off with it leaps and bounds. I don’t think it could have gone any smoother.”
“Sockeye is simple, efficient, and effective at getting the right work scheduled at the right time and with the right employees. I’m just astounded at its ease of use, its simplicity,” said Mike Williams.
Results
Sockeye has enabled Cargill Meat Solutions to:
Extend SAP for maintenance scheduling
Retire delicate, disjointed spreadsheet tools
Optimize scheduling & reliability
Centralize scheduling across 35 facilities
Improve workforce utilization & safety
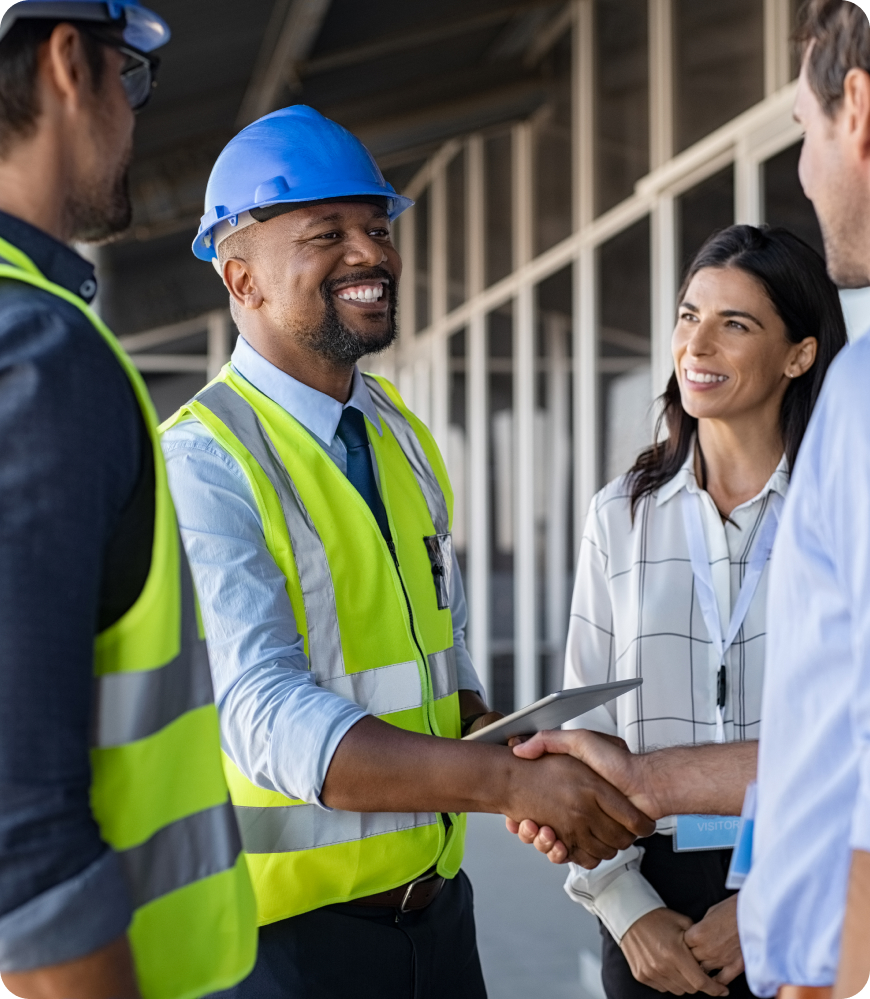
Related Case Study
Sockeye Elevates Cargill’s Operations
Sockeye seamlessly integrated into Cargill’s workflow, effortlessly filling the scheduling gap left by SAP migration. Discover how simplicity, efficiency, and perfect fit made Sockeye the ideal solution.