Maintenance scheduling might not be the most exciting part of your week — but it’s definitely one of the most important. It ensures your team is focused, your equipment runs smoothly, and your budget stays in check.
The challenge? Manually building schedules takes a lot of time. If you want to scale efficiently, maintenance scheduling automation isn’t optional — it’s essential.
In this article, we’ll explore how automation transforms maintenance scheduling, discuss common pitfalls with traditional solutions, and show you how to use Sockeye to create optimized daily and weekly maintenance schedules with just a few clicks.
How maintenance scheduling automation works in a CMMS
Many companies still rely on SAP, Maximo, JDE, and other legacy solutions for maintenance scheduling. These traditional systems typically offer only basic automation, such as scheduling recurring tasks based on frequency (daily, weekly, monthly).
The truth is, you can achieve the same level of automation using Excel — and plenty of maintenance teams do exactly that (despite the disadvantages).
Modern CMMS solutions have taken automation a step further. Platforms like Fiix, Limble, MaintainX, or Hippo offer more advanced options, including condition-based maintenance triggers, automatic notifications, and sometimes even integrations with predictive analytics software.
While these features might sound impressive, they often come at a cost of complexity that slows down your workflow rather than streamlining it. It’s easy to get lost in feature creep, where your maintenance scheduling becomes unnecessarily complicated, overshadowing the initial goals: simplicity and efficiency.
Maintenance scheduling automation should simplify your process, not complicate it. Unfortunately, even modern CMMS platforms miss the mark by focusing too much on features and too little on practicality.
The missing factor: labor availability
Most maintenance scheduling solutions, even those offering advanced automation, miss a crucial factor: data on labor availability. While it’s great to have a system that schedules your tasks automatically, schedules often fall apart — or are grossly inefficient — because they don’t account for the availability of your technicians and contractors.
If the system you are using assigns work without considering who is actually available to do it, you end up with last-minute shuffling, delays, or tasks not getting done at all. Sockeye, our maintenance scheduler system, solves this by directly incorporating labor availability into your maintenance schedules. It pulls real-time availability data straight from your workforce management/HR software, so your schedules always reflect who’s available and who isn’t. If you are not using one, we can set up availability patterns based on your typical work schedule — so only exceptions (sick days, vacations, etc.) need to be updated manually.
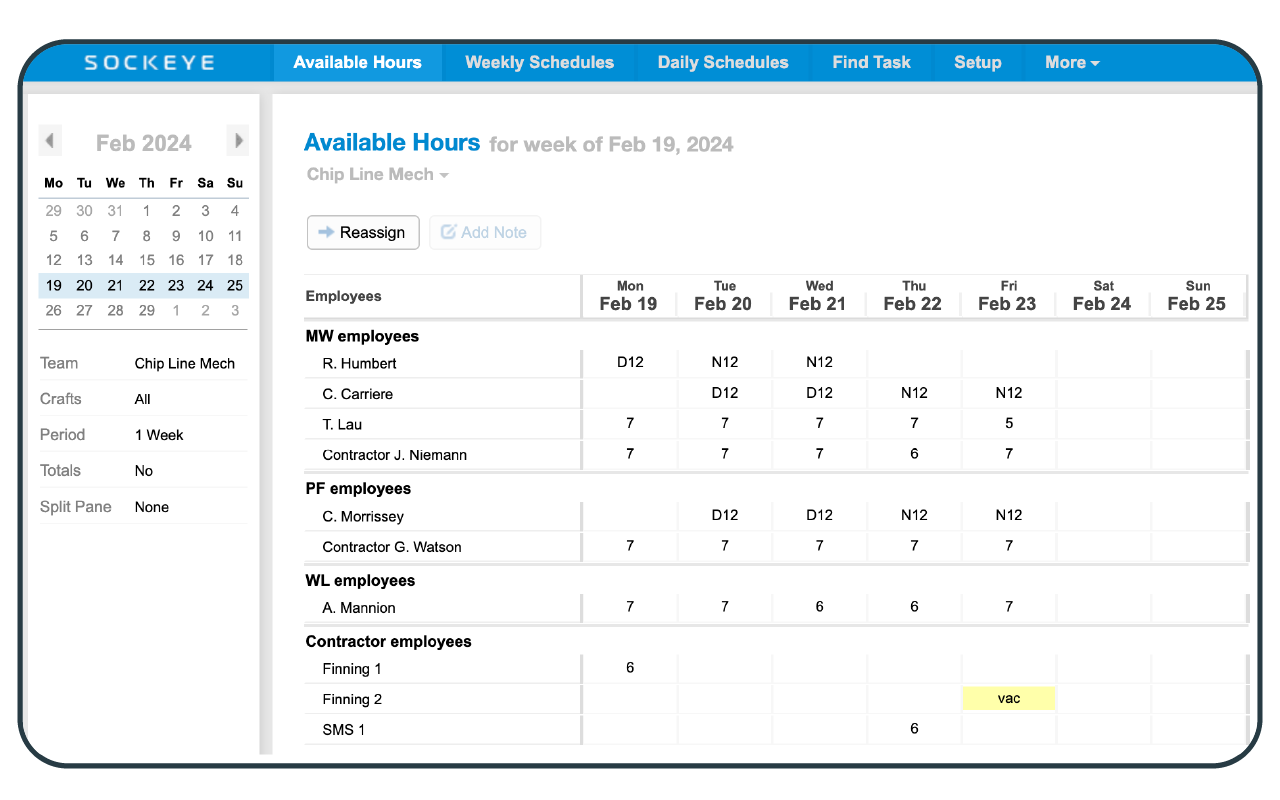
Crew availability hours tab in Sockeye
Let’s see how this comes together to help you automate the creation of weekly maintenance schedules.
Build a weekly maintenance schedule in Sockeye with two clicks
Sockeye is a simple but powerful CMMS bolt-on for maintenance scheduling. Simply connect your CMMS to Sockeye and use our intuitive interface and automation to schedule PMs and WOs. It is perfect for teams that are not satisfied with the scheduling functionality of their existing CMMS or EAM software.
Before you start, the Sockeye team works with you to prepare your environment — help set up users, labor availability, shift patterns, and integrations with your CMMS and HR software.
We do all of the heavy lifting — your IT team will think we are trying to steal their job.
You can try Sockeye for free. The only thing we need from you is a copy of your schedule and one hour of your time.
Here’s how maintenance scheduling typically works for companies that use Sockeye.
Step #1: Upload a list of your maintenance tasks
Before you can leverage Sockeye’s automation, you first need to have a list of tasks that are ready to be scheduled. Usually, this is done by pulling that list from your existing CMMS software.
Don’t worry, this is not done manually. Once we integrate Sockeye with your CMMS, you only need to click a “↻ Refresh” button in Sockeye, and it will automatically update your Backlog in Sockeye with the list of newly available work.
Step #2: Use Sockeye’s automation to create the weekly schedule
Once you have a list of tasks that are ready to be scheduled, this is where the magic happens. First, you will want to select the week of the month and the team you are scheduling for (A Crew in the example below). If you have a big backlog, you can use the search box to quickly find specific tasks you want to schedule. Then, just select those tasks and click the “+Schedule” button.
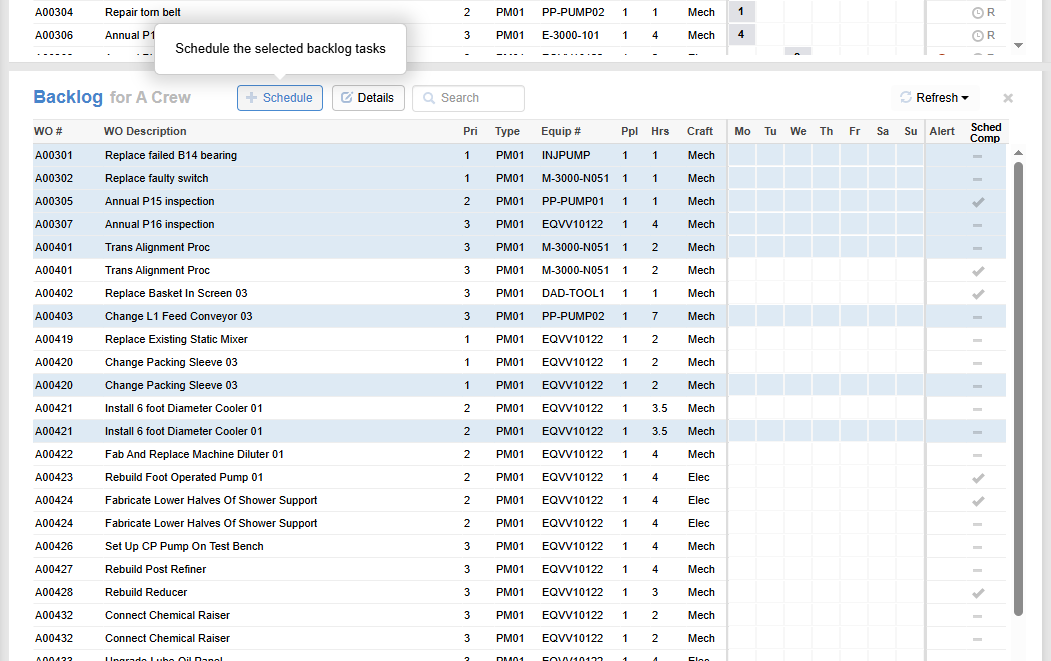
Sockeye will check which team members and contractors are available and automatically build your weekly maintenance schedule.
Alternatively, you can schedule a specific work order on a particular day by simply clicking on the corresponding box under that day of the week. Here’s how that works:
Step #3: Adjust your weekly and daily schedules as needed
After Sockeye builds your schedule, schedulers and supervisors can review it to identify any conflicts or opportunities for efficiencies. There might be adjustments you want to make to account for equipment availability, optimize downtime (perform all work on a piece of equipment in one go to avoid multiple outages throughout the week), make adjustments for specific technician knowledge or experience, and similar.
When you’re finished, you can deploy the schedule so the whole team can see and use it.
Now, maintenance planners and schedulers would have a much easier time if this were the end of the story. Unfortunately, operational realities — like unexpected equipment breakdowns, missing parts, sick days, and production schedule changes — are always ready to hit hard and mess up your schedule.When that happens, you want a tool like Sockeye that simplifies moving work between different crews and dates. You can reschedule work by simply dragging and dropping work orders around. You can also use this functionality to quickly level work between crews.
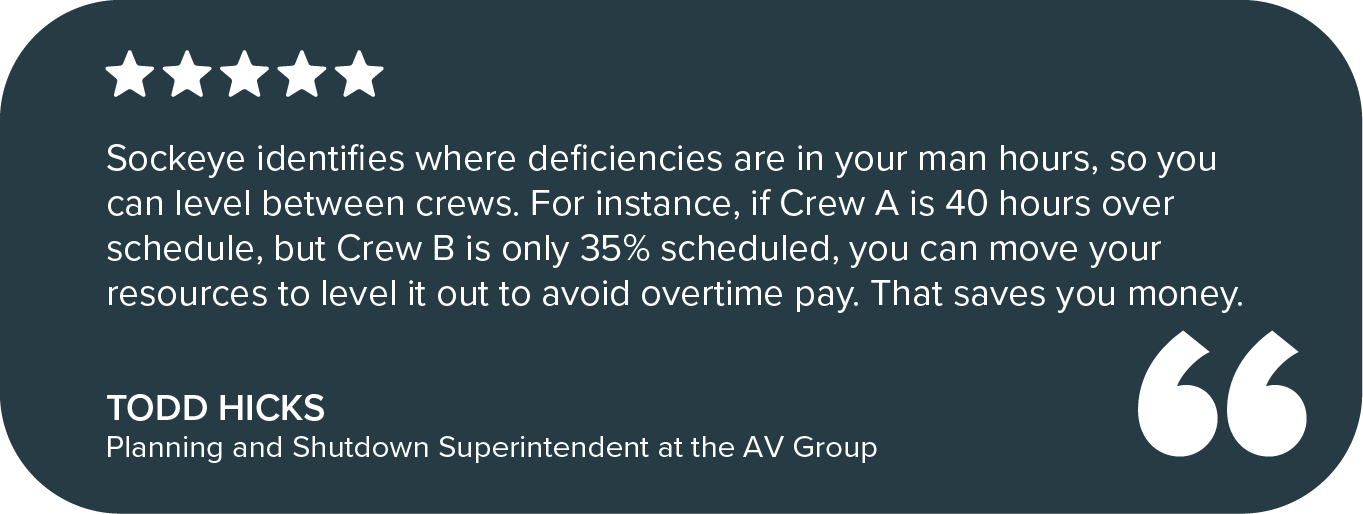
Here’s a quick tutorial that shows this in action:
It’s that simple!
Start automating maintenance scheduling today
If you’re still switching between your CMMS and Excel spreadsheets to schedule work, it’s time to stop. On average, teams that use Sockeye’s maintenance scheduling automation save hours each week on scheduling alone. It’s because what took them hours before can now be done in just a few minutes.
Let’s show you how easy it is to set up and use Sockeye:
- Book a call with our specialist to help us understand your specific needs.
- After that, we can set you up with a demo account. This requires no investment or IT resources — just an hour or two from your scheduler.
- If you like what you see, we will connect Sockeye with your existing CMMS and get you up and running in no time.
Just imagine: Two weeks from now, you would no longer need to fly blind through hours of disjointed scheduling, missing data, and constant complaints. Take Sockeye for a spin and see why we boast an incredible 98% retention rate.
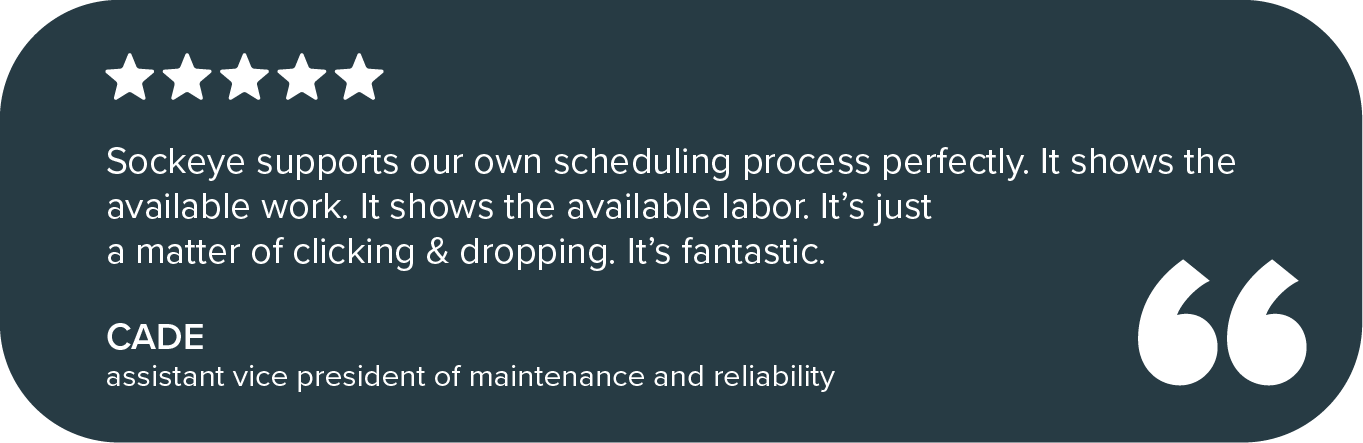