In manufacturing, downtime is any period when production stops — whether planned or unplanned. Every minute your machines aren’t running costs money through lost production, idle labor, and potential ripple effects throughout your operation. For the average manufacturer, this can translate to thousands of dollars per hour in direct losses.
When you reduce downtime, you increase your production capacity while freeing up resources previously spent on firefighting. Oftentimes, the most effective way to minimize machine downtime is to improve how maintenance is planned, scheduled, and executed.
Let’s dive deeper into practical strategies you can implement immediately to see real improvements in equipment reliability, maintenance efficiency, and overall productivity.
Managing different types of machine downtime
Manufacturing downtime is a critical factor that directly impacts your bottom line. Understanding the different types of downtime is the first step toward minimizing it effectively.
All downtime in manufacturing can be broadly categorized into two types: planned and unplanned. Each affects your production differently and requires distinct management approaches.
Planned downtime refers to scheduled interruptions in production that are anticipated and built into your production schedule:
- Preventive maintenance sessions
- Machine setups and changeovers between product runs
- Quality inspections and calibrations
- Scheduled software updates
- Staff training on equipment
Planned downtime is controllable and can be strategically scheduled during low-demand periods to minimize impact on productivity.
Unplanned downtime occurs unexpectedly and disrupts production without warning:
- Sudden equipment breakdowns
- Emergency repairs
- Power outages
- Material shortages
- Unexpected staff absences
Unplanned downtime is particularly costly because it leads to missed deadlines, wasted materials, and idle labor costs.
To effectively reduce downtime in your facility, you need to identify and address its root causes. Some of the primary culprits behind production interruptions include:
- Equipment/asset failure: Worn parts, lack of lubrication, electrical issues, or software glitches cause machines to stop functioning. Regular inspection protocols and condition-based monitoring can help detect potential failures before they occur.
- Human error: Improper machine operation, miscommunication between shifts, or incorrect setup procedures. Implementing standardized training programs and clear documentation can significantly reduce these incidents.
- Utility disruptions: Power outages, compressed air system failures, or water supply interruptions. Backup systems and redundancies for critical utilities can minimize the impact of these disruptions.
- Natural disasters: Floods, fires, storms, or other events that damage facilities or prevent worker access. Having comprehensive disaster recovery plans and appropriate insurance coverage helps manufacturing businesses recover more quickly.
- Process bottlenecks: Imbalances in production flow where one station can’t keep pace with upstream processes. Value stream mapping and production balancing techniques can identify and eliminate these constraints.
Understanding these causes is essential for developing targeted strategies to reduce downtime and improve manufacturing productivity.
How to reduce downtime and improve productivity
Let’s face it — downtime eats into your profits every single minute. But here’s the good news: you don’t need fancy sensors or AI systems to make significant improvements. While they do help, organizations often have fundamental issues they should tackle first.
In the following sections, we’re going to focus on practical, affordable strategies that you can start implementing today. No expensive tech overhauls, just smart adjustments to your existing operations that will help you squeeze more productive hours from your current setup.
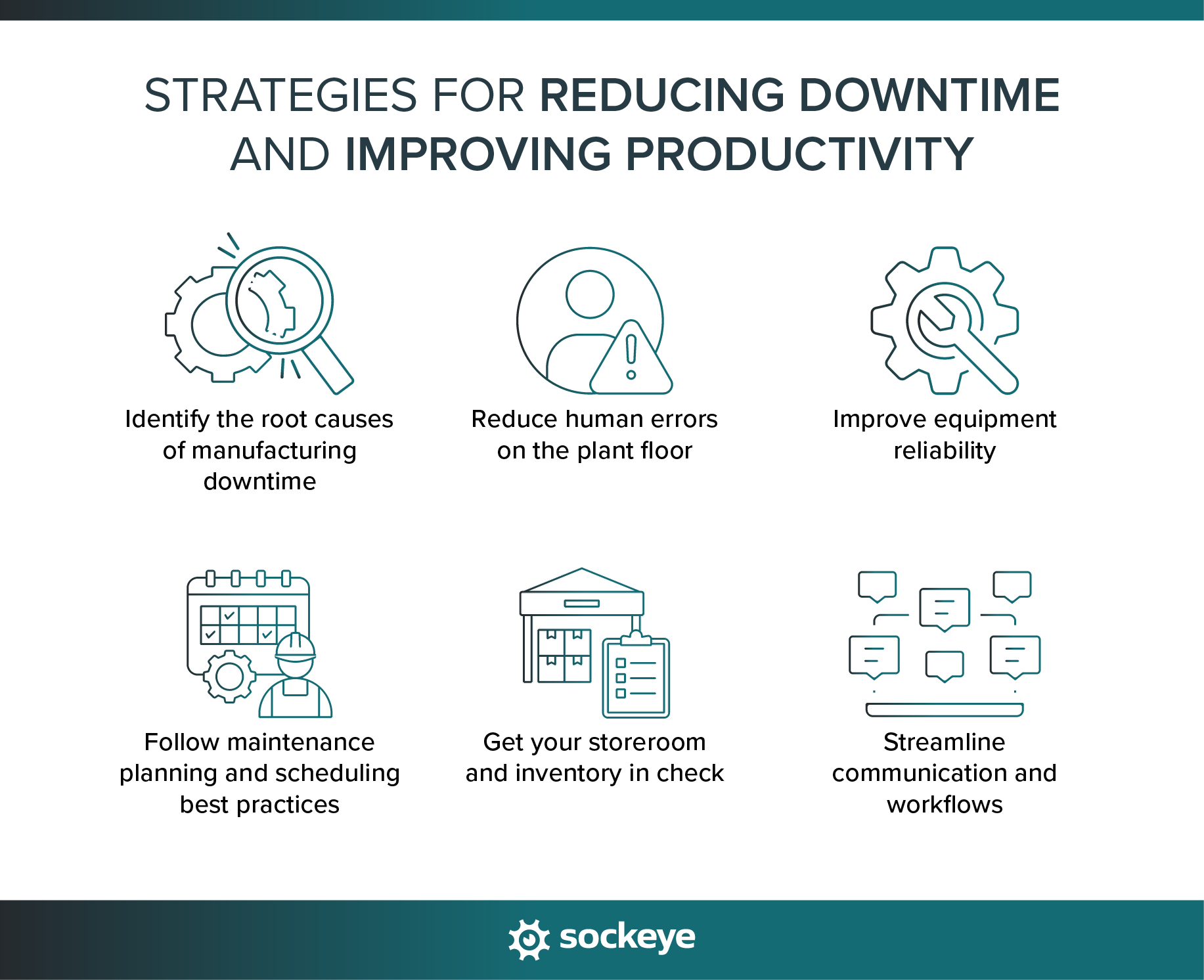
1. Identify the root causes of manufacturing downtime
As we discussed earlier, there are many different causes of downtime. The first step should always be to analyze historical data and try to identify when and why production stops. If that is insufficient, you will need to implement some type of downtime tracking — whether that is done through paper logs, Excel, CMMS, MES, or SCADA.
Once you have enough data, apply Root Cause Analysis (RCA) techniques to identify patterns and underlying issues. Methods like the “5 Whys”, fishbone diagrams, or Pareto analysis can help drill down past symptoms to discover core issues.
After identifying root causes, you can focus on eliminating downtime causes based on their frequency, duration, impact on production, and required resources investment.
The strategies we discuss below aim to eliminate, reduce, or control some of those common causes of downtime.
2. Reduce human errors on the plant floor
Human errors are behind many of your unplanned downtime incidents. A new operator presses the wrong button, maintenance doesn’t coordinate with production, a technician skips a critical step during routine servicing, or the night shift isn’t told about a machine quirk during a shift changeover.
These seemingly small errors can bring production to a costly halt.
Aside from digitizing processes, the most effective way to cut these mistakes dramatically is to create clear, detailed SOPs that leave no room for guesswork. Make sure these guides aren’t buried in some binder in the manager’s office — they should be right at the workstation or accessible with a tablet/phone, complete with photos or diagrams showing exactly what to do.
This process standardization needs to be paired with proper communication and training. Make sure everyone gets thorough hands-on training — not just when they’re hired, but regularly throughout their employment.
3. Improve equipment reliability
Instead of waiting for equipment to fail, implement preventive maintenance schedules based on manufacturer recommendations, equipment usage, and your own historical data. Better yet, consider condition-based maintenance for critical equipment to monitor indicators that signal potential issues.
The repair-or-replace decision is one many manufacturers struggle with. Often, equipment that seems “good enough” is draining resources through frequent repairs and inefficiency. A good rule of thumb: when annual maintenance costs exceed 20% of replacement cost, consider replacement. Before that, you should make sure that those costs and downtime happen because the equipment in question is old and worn out.
Many newer machines include built-in diagnostics that can alert your maintenance planners and schedulers about potential problems. While the initial investment may be substantial, the reduction in downtime, energy costs, and maintenance expenses often provides a surprisingly quick return on investment.
4. Follow maintenance planning and scheduling best practices
With reactive or poorly scheduled maintenance, you’re facing a double hit — unplanned downtime when equipment fails unexpectedly, plus inefficient use of maintenance resources. When technicians rush from one emergency to another, repairs take longer, costs skyrocket, and your production schedule suffers.
Want to break this cycle? Start by getting your maintenance and production teams to talk regularly. Schedule joint planning meetings where production can highlight their critical periods while maintenance identifies equipment needs. This teamwork helps you find those perfect maintenance windows that won’t disrupt your production targets.
Focus on these best maintenance practices for planning and scheduling:
- Assign a dedicated planner
- Create clear job plans
- Keep detailed equipment records
- Manage your parts inventory
- Prioritize work orders based on equipment criticality
- Match tasks to technician skills
- Set realistic timeframes
- Track your schedule compliance
We have seen dozens of organizations struggle with downtime because of poor scheduling. This happens because maintenance teams do not have proper insight into technician availability — some techs get too much work while others get too little. Critical tasks get missed or delayed, and equipment reliability goes down.
This is why maintenance teams need maintenance work order scheduling software instead of using Excel or whiteboards. They can assign work based on technician skills and real-time availability, which means more work can be scheduled and done with the existing resources.
5. Get your storeroom and inventory in check
Equipment sitting idle because the right part isn’t available is egregious because it is often preventable. Even worse is when the part is somewhere in your facility, but your maintenance team wastes hours each month hunting through disorganized shelves or multiple storage locations. This negatively affects both planned and unplanned downtime.
Ideally, you would have a CMMS or dedicated inventory software to track what you have, where it’s located, and when to reorder. Set minimum stock levels for critical parts based on usage history and lead times. A well-organized storeroom with clear labeling and barcode scanning can cut parts retrieval time from hours to minutes. You can further speed things up by creating maintenance kits — a bag/package containing tools and parts needed for the scheduled job.
Identify your most reliable vendors and work to become their preferred customer. Negotiate service agreements with guaranteed delivery times for critical components. Consider consignment arrangements where suppliers maintain inventory on your site at no cost until you use it. These partnerships can turn potential week-long outages into short disruptions.
6. Streamline communication and workflows
Create clear approval chains with designated backups for each position to keep things moving when the primary decision-maker is unavailable. Establish spending thresholds that empower frontline managers to make immediate calls on repairs below certain dollar amounts.
Leverage digital tools to speed up communication during critical events. Group messaging apps and video calls can connect maintenance, operations, and management instantly when problems arise. These tools eliminate the “I didn’t know” factor that often extends downtime unnecessarily.
Develop a written emergency response plan that everyone knows by heart. Detail exactly who does what when critical equipment fails — who assesses the situation, who secures replacement parts, who communicates with customers and top management about potential delays.
Lastly, encourage team collaboration and feedback loops. Operators often notice subtle changes in equipment performance. Maintenance teams understand repair challenges that operations might not consider. When these groups regularly share insights, you’ll catch potential issues earlier and develop more effective solutions together.
Minimize downtime and improve productivity with effective scheduling
Effective scheduling plays a crucial role in minimizing downtime and maximizing productivity. By prioritizing proactive work, coordinating production and maintenance schedules, and leveraging the right tools to assign tasks efficiently, manufacturers can prevent many costly disruptions.
A surefire way to get more work done is to schedule more work. With a tool like Sockeye, you can track available technician hours and scheduled work in real time. This allows you to schedule at or close to 100% of your available hours with confidence.
Implementing structured planning meetings, optimizing work order management, and maintaining an organized inventory system ensures that technicians have what they need when they need it.
If your team struggles to schedule more work, see what Sockeye can do for you.