Maintenance teams rely on schedules to reduce downtime and avoid costly breakdowns. But planning work is only half the battle — ensuring that planned maintenance actually gets done on time is just as important. That’s where schedule compliance comes in.
It’s a simple but powerful metric that helps maintenance schedulers and managers understand if work is being completed as expected or if delays and inefficiencies are creeping in.
In the following paragraphs, we will discuss what maintenance schedule compliance tells you about your operations and how to efficiently calculate and track this important scheduling metric.
What does schedule compliance mean?
Schedule compliance is a maintenance metric that measures how much of the planned maintenance work is completed within the scheduled timeframe. It’s a way to track whether teams are staying on top of their maintenance work or if delays and disruptions are throwing off the schedule.
A well-maintained facility or plant relies on planned maintenance to prevent breakdowns and unexpected failures. When maintenance schedule compliance is high, it means work is getting done on time, reducing the risk of equipment failures and costly downtime. On the flip side, poor schedule compliance can lead to backlogs, inefficiencies, and a higher chance of emergency repairs.
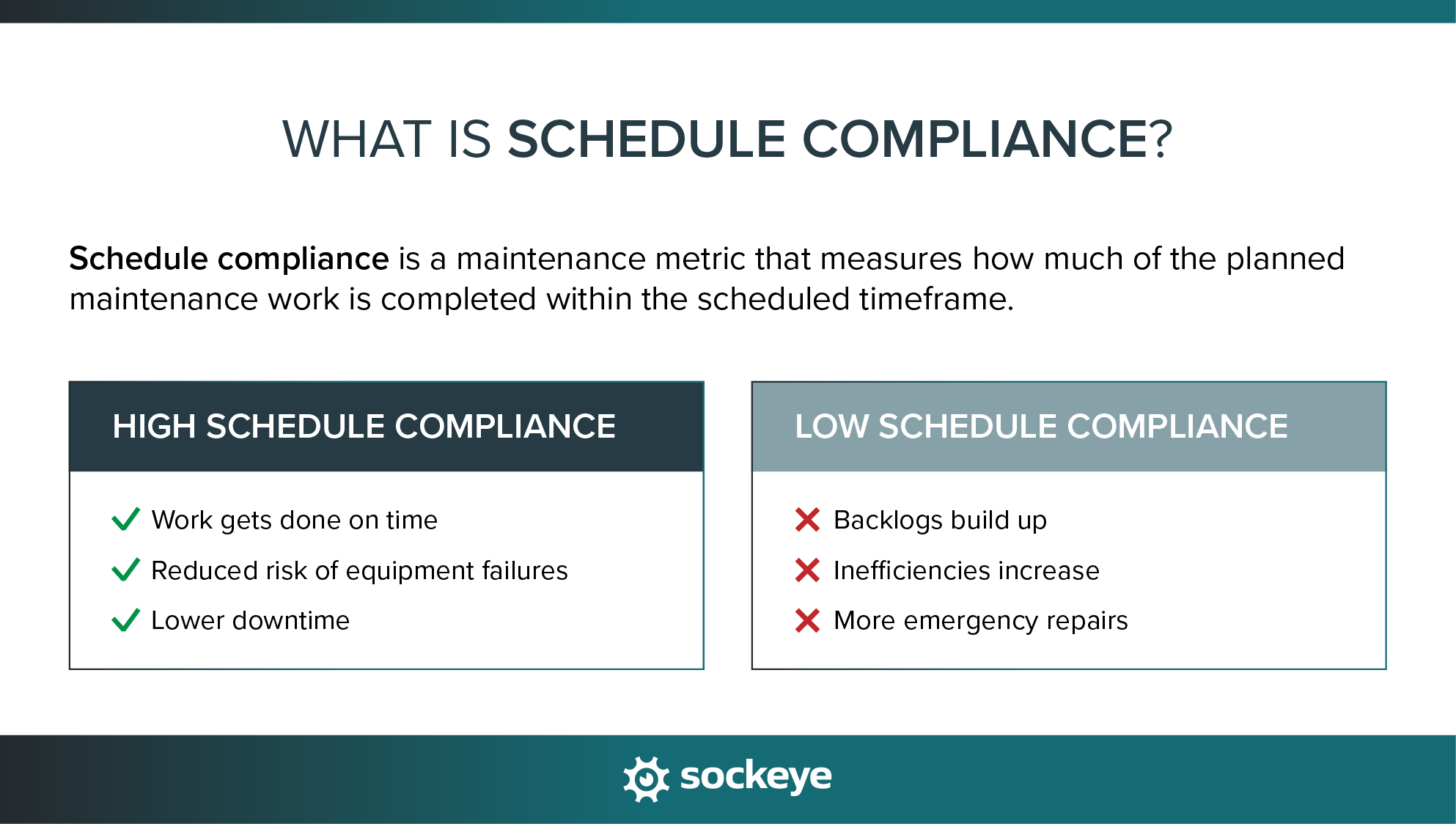
There are a few misunderstandings about schedule compliance that can lead to misinterpretation of the metric:
- It doesn’t measure efficiency — just adherence to the plan. A high compliance rate doesn’t always mean maintenance is running efficiently. It only shows that scheduled tasks are being completed on time.
- A perfect 100% compliance rate isn’t always realistic. Unexpected breakdowns, staffing shortages, or urgent work orders can shift priorities. Still, world-class maintenance teams should aim to stay at or above 90% compliance as a benchmark.
- It shouldn’t be viewed in isolation. Compliance should be analyzed alongside other maintenance KPIs like Mean Time Between Failures (MTBF) or work backlog to get a full picture of performance.
Using schedule compliance to improve maintenance efficiency
Schedule compliance isn’t just a number — it’s a tool that can help maintenance teams work smarter. It can help managers identify inefficiencies, balance workloads, and improve overall maintenance effectiveness. Here’s how.
1. Identify bottlenecks
If schedule compliance is consistently low, it’s a sign that something is slowing the team down. Common culprits include:
- Frequent delays due to waiting on parts or approvals.
- Work orders not being completed due to insufficient labor.
- Poor scheduling practices that overload technicians.
By spotting trends in compliance data, teams can pinpoint bottlenecks and address them — whether that means improving parts inventory management, streamlining approval processes, or rebalancing workloads.
2. Balance preventive and reactive maintenance
Low schedule compliance can indicate that too many emergency work orders are pulling technicians away from planned tasks. If reactive maintenance is taking over, preventive maintenance (PM) may suffer, leading to long-term equipment reliability issues.
By monitoring schedule compliance alongside emergency work trends, managers can find the right balance — ensuring preventive maintenance gets done while still handling urgent repairs efficiently.
To make this easier, maintenance scheduling tools like Sockeye automatically track relevant metrics like Hours spent on reactive work and Hours spent performing preventive work.
3. Improve resource allocation
A drop in compliance might signal a need for better resource planning. If maintenance teams frequently miss scheduled tasks, it could be due to:
- Labor shortages (not enough technicians to complete planned work)
- Inefficient shift scheduling (overloading certain time slots)
- Material shortages (waiting for parts to arrive)
By analyzing compliance data, managers can adjust work schedules, allocate resources more effectively, and ensure materials are available when needed.
Again, having maintenance software at your disposal helps you drill down into your data to uncover root causes. For instance, Sockeye lets you add “delay notes” to each WO that has been postponed. Similarly, since our maintenance scheduling system is based on real-time worker availability, it’s easier to discern when poor schedule compliance is caused by labor shortages and inefficient scheduling.
Schedule compliance formula and calculation
The standard formula for calculating schedule compliance is simple: you just need to divide the number of WOs completed on time by the total number of scheduled work orders — and multiply that by 100 to get a percentage.

Here are a few key points to consider for this calculation:
- Partially completed tasks don’t count: Only fully completed work orders are considered in the calculation.
- Excludes unscheduled work: Emergency or corrective work orders that were not part of the original schedule aren’t factored in.
- Timeframe matters: The calculation should be done for a specific period (week, month, or quarter) to track trends accurately.
Now, let’s apply this formula to real-world scenarios.
Example #1: Monthly Preventive Maintenance Compliance
Let’s say a maintenance team scheduled 100 preventive maintenance (PM) work orders for the month. At the end of the month:
- 85 work orders were completed on time
- 15 work orders were completed late
- 5 work orders were missed entirely
Using the schedule compliance formula:
Schedule Compliance = (80 / 100) x 100
Schedule Compliance = 80%
What this tells us: The team successfully completed 80% of the scheduled work orders on time. The remaining 20% indicates potential inefficiencies or resource constraints. A deeper analysis is needed to understand why the late/missed work orders occurred — was it due to labor shortages, emergency work, or parts unavailability?
Example #2: Mixed PM and reactive work
In this scenario, a maintenance team scheduled 120 work orders for a facility over a month. These included both preventive maintenance and planned corrective work. At the end of the month:
- 90 work orders were completed on time
- 15 work orders were completed late
- 10 work orders were canceled
- 5 work orders were missed entirely
Using the schedule compliance formula:
Schedule Compliance = (90 / 120) x 100
Schedule Compliance = 75%
What this tells us: Three out of every four scheduled work orders were completed on time. The 15 late work orders indicate potential scheduling or resource issues. The 5 missed work orders could mean they were deprioritized or lacked necessary materials. The 10 canceled work orders do not affect compliance, since only scheduled work that was supposed to be completed is considered.
Using the 10% rule to give your team some wiggle room
The 10% rule allows for a small buffer in PM schedule compliance calculations. Instead of strictly marking a PM as late if it isn’t completed by the scheduled date, the 10% rule allows for some flexibility based on the scheduling interval.
How it works:
- If a PM has a 10-day completion window, it can be completed up to 1 day late and still count as “on time.”
- If a PM occurs monthly (has a 30-day interval), you allow for up to a 3-day delay (10% of 30). So even if the PM is completed 2 or 3 days late, you still consider it as completed “on time”.
This approach recognizes that minor scheduling delays happen but shouldn’t drastically impact maintenance performance.
Pros of incorporating this rule: Provides flexibility for minor delays that don’t impact operations or reliability. Prevents unnecessary penalties for small scheduling shifts.
Cons of using this rule: If not monitored, it can create a culture of leniency where delays become normalized. It may also hide inefficiencies if teams constantly rely on the grace period instead of trying to adhere to the schedule.
How to track schedule compliance effectively
The first thing you will need to do is to ensure accurate data entry. Before technicians mark a WO as “completed”, they should double-check that they have selected the right completion date.
Manually tracking compliance with spreadsheets is possible but can be time-consuming and prone to errors. Modern maintenance tools — like a CMMS or Sockeye — let you automatically log work order status, completion times, and completion rates. At any time, you can log in to review schedule compliance for a selected period.
In the screenshot below, you can see the schedule compliance report that Sockeye automatically generates for teams that use it for scheduling maintenance work.
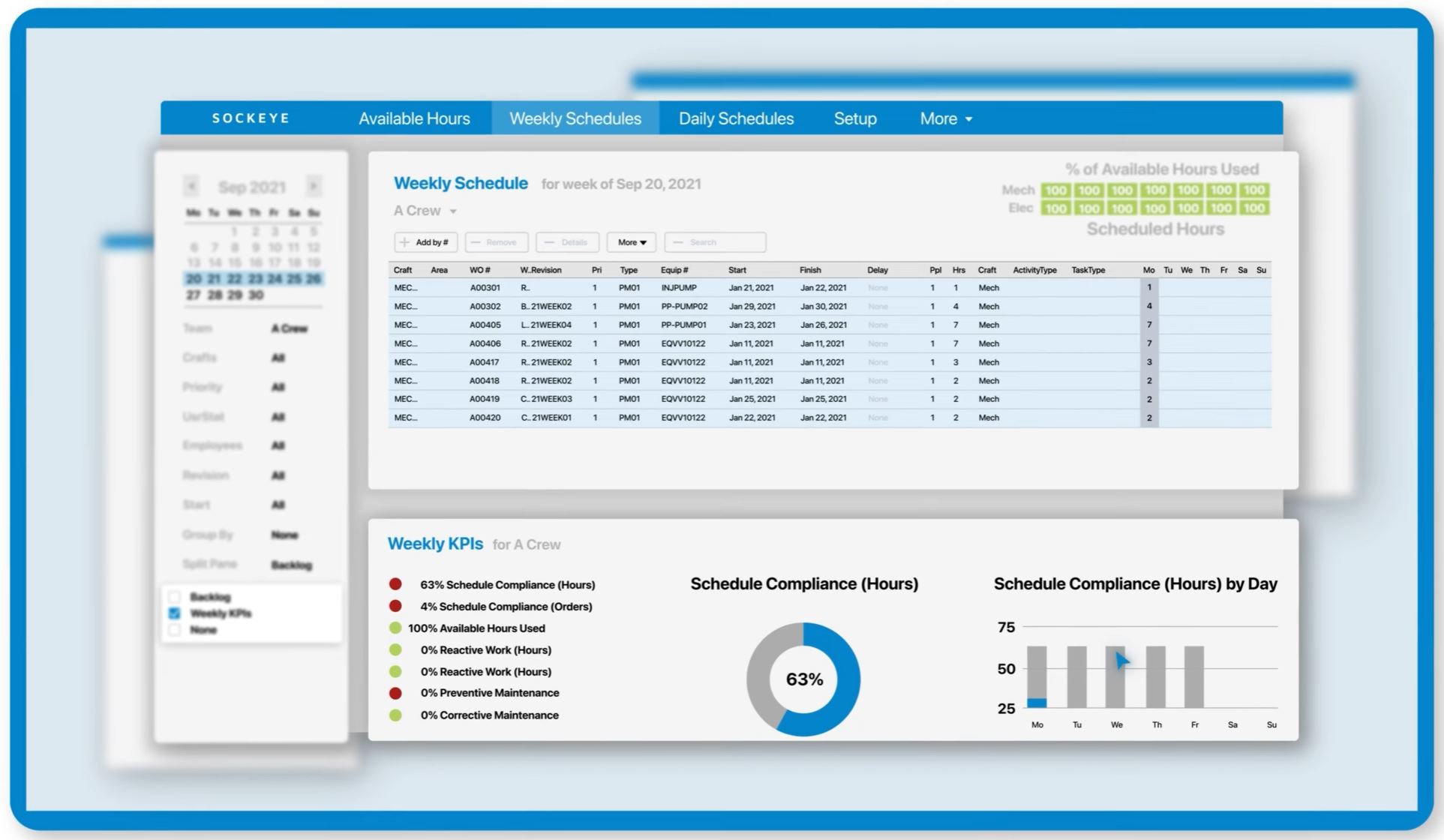
Schedule compliance as a KPI: Common pitfalls to avoid
Tracking schedule compliance is a great way to measure maintenance performance, but relying too heavily on this KPI can lead to misleading conclusions. Below are some common pitfalls to watch out for:
Focusing only on the percentage
A high schedule compliance percentage looks good on paper, but it doesn’t always mean maintenance is running efficiently. If compliance is 95% but the equipment is still breaking down frequently, the maintenance strategy may be flawed.
What to do instead:
- Pair schedule compliance with other KPIs like MTBF, MTTR, Available scheduling hours used, and Hours spent clearing out deferred maintenance work.
- Analyze why work orders are being completed on time — is it because the schedule is realistic, or because teams are skipping steps to hit targets?
Manipulating data to hit compliance targets
If schedule compliance is treated as the only measure of success, teams might find ways to game the system. Common issues include:
- Closing work orders before they’re done just to meet deadlines.
- Rescheduling overdue work orders instead of marking them as late.
- Not logging unscheduled work to avoid lowering the compliance rate.
What to do instead:
- Emphasize accuracy over perfection — it’s better to have honest numbers than an inflated compliance rate.
- Ensure work order closure processes require actual completion, not just paperwork.
- Use compliance trends to improve scheduling, rather than punishing teams for missing deadlines.
Neglecting unscheduled work
Emergency repairs and unscheduled corrective work are a reality in any maintenance operation. If schedule compliance is the primary focus, it might ignore or de-prioritize important repairs that weren’t on the original schedule.
What to do instead:
- Track and analyze unscheduled work separately to understand how much reactive maintenance is happening.
- Look at the ratio of planned vs. unplanned work — if too much effort is going toward emergency repairs, it’s a sign that preventive maintenance needs improvement.
- Use compliance data in context rather than treating it as an absolute measure of success.
Schedule compliance is valuable, but only if used correctly. Instead of chasing a perfect compliance rate, teams should focus on what the data actually reveals about maintenance efficiency, scheduling accuracy, and overall reliability.
Automate schedule compliance tracking with Sockeye
Sockeye is a simple CMMS add-on that companies use to schedule and track maintenance work. While CMMS solutions do many things right, scheduling is rarely one of them. They make it so rigid or complicated that teams go back to using spreadsheets.
Sockeye helps you fill that gap. It integrates with your existing CMMS system to simplify scheduling. And as a scheduling tool, Sockeye has built-in analytics and reporting for various scheduling KPIs – schedule compliance included.
Here is how the reporting looks in Sockeye:
If tracking compliance manually is slowing your team down, Sockeye can help automate and simplify the process. With real-time insights, maintenance teams can stay ahead of scheduling issues and reduce delays.
Want to see Sockeye in action? Schedule a quick demo or reach out to our support team.