Maintenance scheduling is the backbone of effective asset management. Done right, it ensures equipment is available when you need it, cuts down on unexpected downtime, and boosts the reliability of every machine on the shop floor.
However, organizing maintenance schedules isn’t always straightforward. Resource constraints, unexpected breakdowns, and the tricky balance between planned and unplanned maintenance create constant challenges.
In this article, we’ll break down 11 best practices that will help you create efficient, adaptable schedules — ones that will keep your team prepared, aligned, and on track.
But first, a quick definition to make sure we’re on the same page.
What is maintenance scheduling?
Maintenance scheduling is the process of organizing and assigning specific maintenance tasks to ensure equipment runs smoothly and without unexpected interruptions. It focuses on deciding when certain maintenance work is going to be performed and by whom.
Unlike maintenance planning — which centers on the overall strategy, resources, and preparations for maintaining assets — scheduling hones in on the timing and sequence of these tasks.
In other words, maintenance planning involves determining “what” needs to be done and “how,” while maintenance scheduling answers “when” and “by whom.”
Together, these two functions keep maintenance work organized, timely, and aligned with business goals.
How does scheduling maintenance save time and money?
Proper maintenance scheduling isn’t just about keeping equipment in good shape — it’s also a powerful way to save time and money. Efficient scheduling can:
- Lower downtime: Regular maintenance prevents unexpected failures, keeping operations running smoothly with minimal interruptions.
- Prevent costly breakdowns: Catching and fixing small issues early avoids expensive repairs or equipment replacements.
- Reduce the need for emergency repairs: Planned maintenance eliminates the high costs associated with urgent, last-minute fixes.
- Better manage resources like labor and spare parts: Scheduling maintenance in advance ensures the right personnel and materials are available, reducing inefficiencies and waste.
- Improve workforce productivity: Employees can work without unexpected delays, leading to higher efficiency and overall output.
- Minimize compliance and safety risks: Well-maintained equipment reduces the likelihood of accidents and ensures adherence to safety regulations, avoiding fines or legal consequences.
In short, a well-organized maintenance schedule not only boosts asset reliability but also directly contributes to the bottom line.
Best practices for scheduling maintenance work
Effective maintenance schedules don’t happen by accident. They require a strategic approach to make sure the right work gets done at the right time with the right resources.
Let’s explore some of the best practices that successful teams use to keep their maintenance schedules running like clockwork.
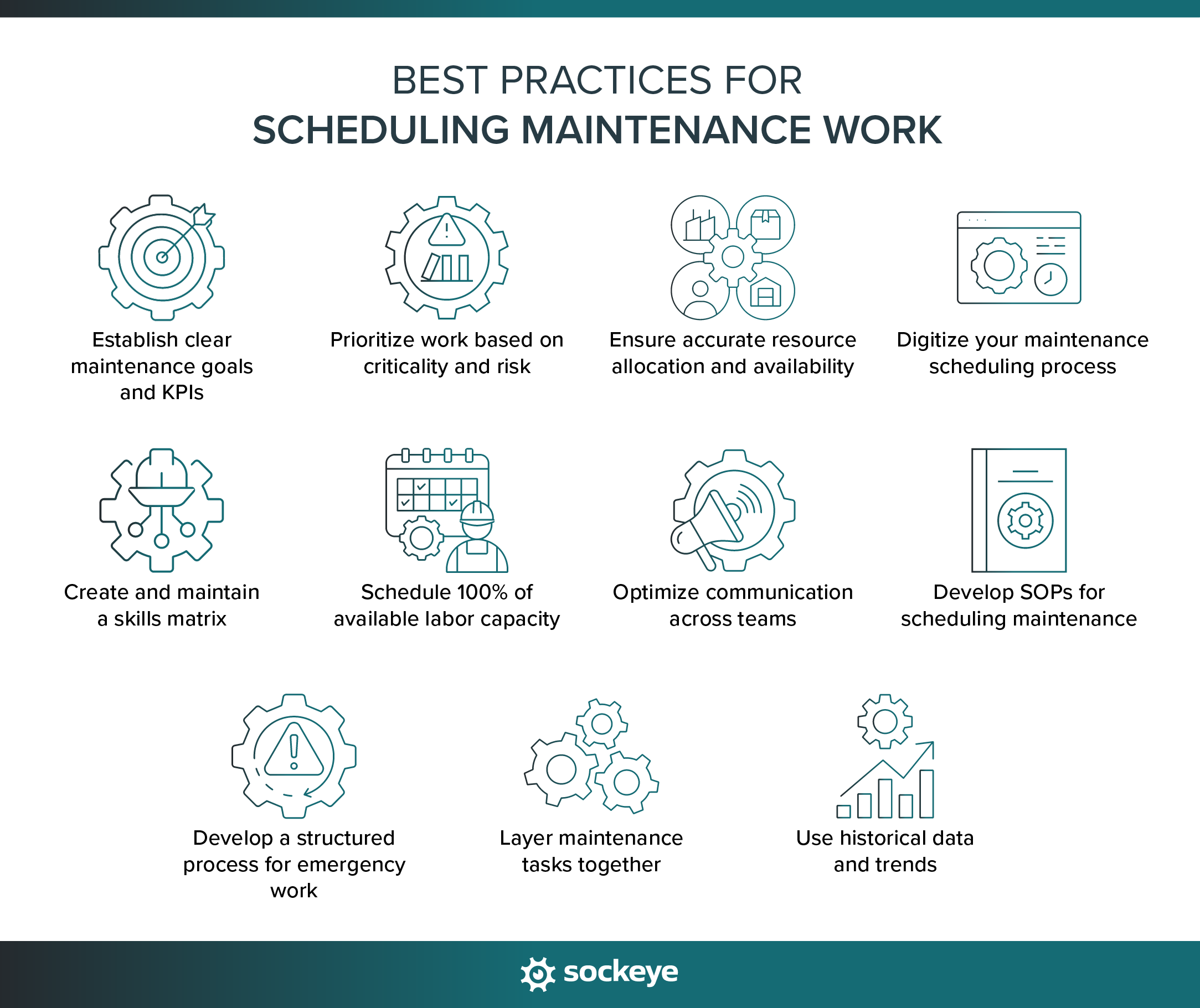
1) Prioritize work based on criticality and risk
Not all maintenance tasks are created equal. By prioritizing work based on criticality and risk, schedulers can allocate resources where they matter most. This ensures that high-impact tasks receive attention first.
A common way to prioritize is through risk-based prioritization or asset criticality analysis, where tasks are ranked based on factors like the potential impact of a failure on operations, safety, and costs.
For instance, maintenance for a CNC machine might be prioritized over non-essential equipment, especially if failure would halt production or compromise safety. For a scheduler to be able to do that effectively, the maintenance and reliability teams first need to get together and create the equipment risk matrix.
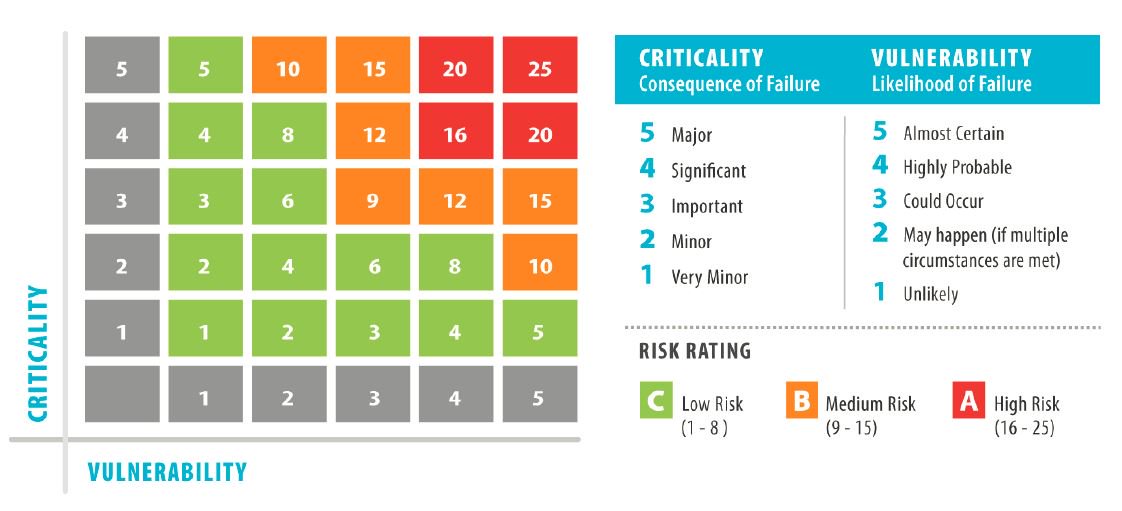
2) Ensure accurate resource allocation and availability
Without accurate resource allocation, even the best-planned schedules can fall apart. That’s why it’s essential to account for technician availability, the necessary spare parts, and any specialized tools required for each task.
Techniques like capacity planning and resource leveling can help here. Capacity planning allows you to assess the workload against available resources, while resource leveling smooths out demand to avoid bottlenecks and reduce idle time. Ideally, your maintenance software and logs can provide you with the historical information you need for such assessments.
As an example, maintenance scheduler apps like Sockeye can provide real-time insights into crew and contractor availability:

A screenshot of the “Available hours” functionality from the Sockeye app.
3) Digitize your maintenance scheduling process
Scheduling maintenance manually or using a spreadsheet leads to inefficiencies, miscommunication, and missed deadlines. We’ve seen it hundreds of times.
There is a reason why so many companies are switching to CMMS and other software — it makes it easier to track progress, set reminders, automate routine scheduling, and adjust schedules on the fly. Now, the problem is that many CMMS solutions are just too cumbersome to use, especially if the only thing you really need is to schedule maintenance work. If you’re in a similar position, check how Sockeye can cut your scheduling time in half.
4) Create and maintain a skills matrix
Understanding each technician’s strengths and skill sets is crucial for efficient scheduling. A simple way to do that is to keep an updated skill matrix for technicians (and even machine operators if they are involved in maintenance work). The matrix should outline each technician’s certifications, specializations, and experience levels. This way, schedulers can assign tasks to the right people, improving both the quality and efficiency of maintenance work.
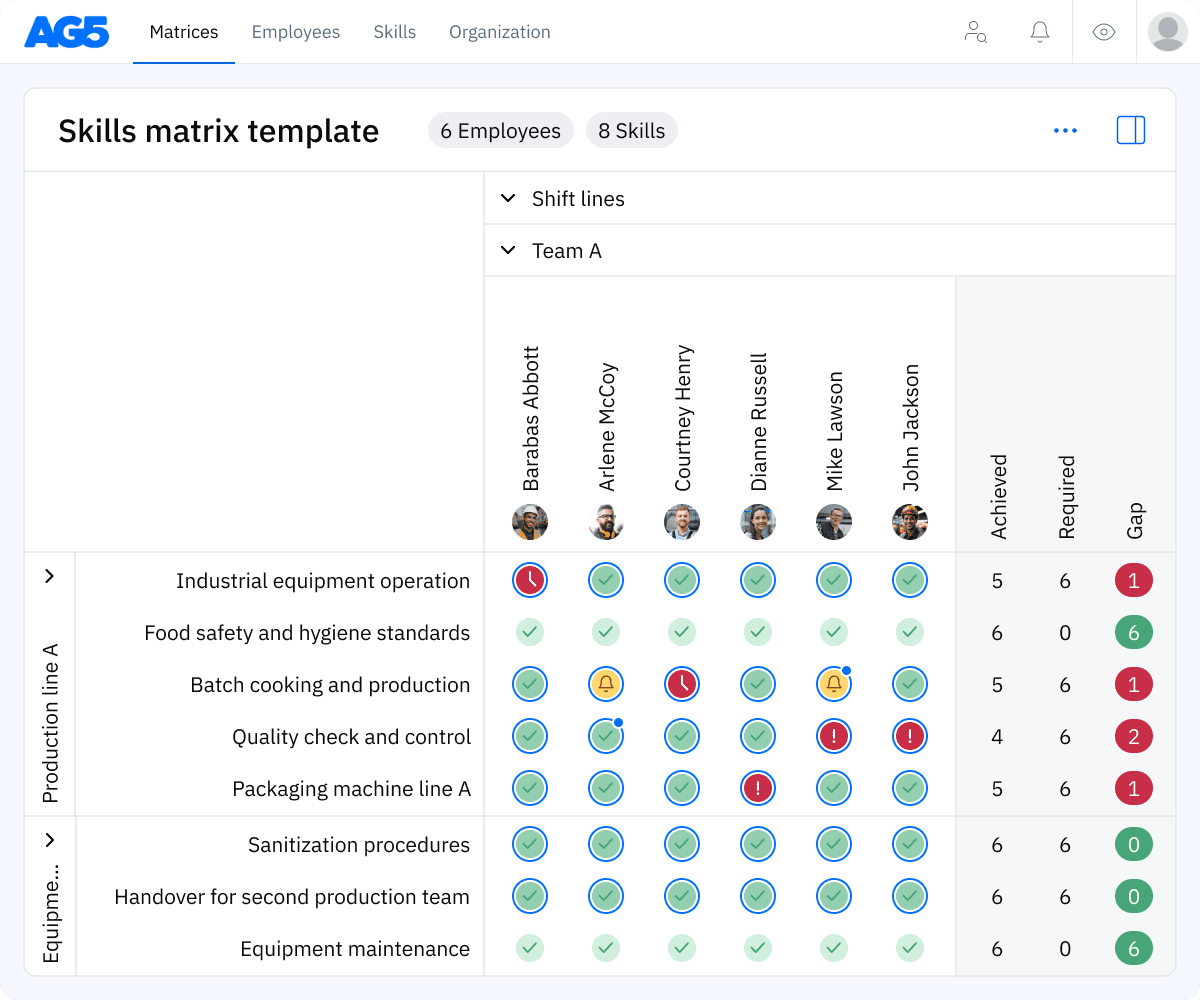
An example of a skills matrix. Source: AG5
Let’s say you have a task that requires advanced electrical troubleshooting. A skills matrix would allow the scheduler to quickly identify qualified technicians, and then assign work based on their availability.
5) Schedule close to 100% of available labor capacity
According to Parkinson’s Law, “The amount of work assigned will expand to fill the time available.”
As Doc Palmer, the author of McGraw-Hill’s Maintenance Planning and Scheduling Handbook, nicely puts it in his MRO Magazine article:
“If a 10-person crew with 400 hours of labor capacity available is expected to do only 200 hours’ worth of work, that 200 hours of work will take 400 hours of labor”.
The idea is that, if technicians are only assigned 80% of their available time, they may (even unconsciously) stretch tasks to fill their shift, leading to wasted time.
He also goes on to say:
“In fact, experience shows that a 10-person crew with 400 hours of available labor capacity that starts with a weekly schedule of 400 hours of specific work orders will complete more work than normal, even if it does not complete all the scheduled work“.
This is one of the reasons why we recommend scheduling close to 100% of available labor capacity. And, if you’re using Sockeye, our tool can do that for you automatically, after which you can review and adjust the weekly/daily schedule as you see fit. If you’re not doing so already, build up slowly. Increase the percentage of scheduled work month-over-month according to what you think is realistic. For example, an aluminum company used Sockeye to go from 37% to 87% of scheduled work by slowly increasing the amount of scheduled maintenance work each month.
6) Optimize communication across teams
Effective maintenance scheduling relies on clear, consistent communication between maintenance, operations, and inventory teams. Miscommunication can lead to scheduling conflicts, delays, or resource shortages, so keeping everyone on the same page is essential.
Here are some ways to facilitate good communication:
- Regular team check-ins, such as morning meetings or weekly schedule reviews, can help teams align priorities and address any issues proactively.
- Using a centralized system, like a CMMS and Sockeye, can further streamline communication by providing real-time access to schedules, work orders, and inventory levels.
- Maintenance schedulers should also feel comfortable reaching out to planners, technicians, or operators if additional information is needed before finalizing a schedule. Simple messaging apps like WhatsApp, Viber, MS Teams, or even Slack can help keep open communication lines between these parties.
7) Develop SOPs for scheduling maintenance
Standard Operating Procedures (SOPs) are often used to standardize and streamline inspections, troubleshooting, and other maintenance work. But there is no reason why you shouldn’t use SOPs to bring the same consistency and clarity to maintenance scheduling.
With these procedures written down, schedulers get a reliable framework for handling routine scheduling tasks, from prioritizing and assigning tasks to tracking completions.
Experience schedulers can check SOPs for a refresher, while newcomers to the scheduling team can use them to get up to speed faster.
Creating SOPs doesn’t have to be complicated — start by documenting existing procedures, then refine them based on input from the team. Over time, this will lead to smoother scheduling, making maintenance operations more efficient and predictable.
8) Develop a structured process for emergency work
A well-defined process for handling emergency work orders can make a world of difference when a critical piece of equipment breaks down. This structured workflow should outline the steps for identifying, prioritizing, and assigning emergency work, as well as any protocols for communicating with relevant teams.
For instance, the workflow might designate specific team members to assess and assign emergency work orders immediately, bypassing the typical scheduling process.
9) Layer maintenance tasks together
If you are focusing on preventive maintenance, you’re probably trying to proactively create weekly and daily schedules, as well as plan for major monthly/quarterly/yearly overhauls that require planned shutdowns.
A simple way to improve efficiency is to try and layer different maintenance tasks together, especially when they require planned shutdowns. By aligning weekly, monthly, quarterly, and yearly maintenance work, schedulers can reduce the number of equipment shutdowns and maximize maintenance time during planned downtimes.
For example, if a yearly inspection requires a complete shutdown of a production line, it’s often a good opportunity to reschedule any weekly or monthly maintenance tasks for that asset to that same day.
10) Establish clear maintenance goals and KPIs
If you change your scheduling practices today, how would you measure the impact of those changes? The only reliable way is to set clear goals and KPIs. According to the MaintainX 2024 report, the most widely used KPI is the preventive maintenance completion rates (56%), closely followed by work order backlog (53%).
By defining measurable targets — like equipment uptime, schedule compliance, preventive maintenance completion rates, and scheduled capacity utilization — maintenance teams get a compass guiding their decisions and helping them evaluate schedule effectiveness.
For instance, if a plant sets a KPI for 95% uptime on a production line, the maintenance team can prioritize preventive tasks for that equipment. KPIs like this not only shape daily scheduling decisions but also make it easier to gauge whether the maintenance schedule is achieving its objectives.
11) Use historical data and trends
Leveraging historical maintenance data allows schedulers to make more informed decisions. By analyzing data on past equipment failures, seasonal trends, and the frequency of specific maintenance tasks, schedulers can optimize future schedules and anticipate peak maintenance periods.
So, if data shows that a specific piece of equipment tends to require more attention during summer, you can proactively schedule more preventive work during those months.
Using historical trends to guide scheduling keeps the maintenance plan data-driven, easier to manage, and responsive to the unique needs of your equipment and facility.
Simplify maintenance scheduling with Sockeye
Sockeye makes building effective daily and weekly schedules fast and easy, even for those with minimal tech experience. With its intuitive interface and automation features, you can create weekly/daily schedules in minutes, without needing extensive training.
By integrating seamlessly with your existing CMMS and workforce management software, Sockeye keeps your schedule up-to-date and ensures you know exactly who’s available and what tasks need attention. Schedulers can easily search, filter, and update the schedule while providing the entire facility with a live, verified schedule.
Here’s a quick 2-minute video that explains how Sockeye simplifies the scheduling process:
Interested in learning more? Book a demo to see Sockeye in action and get answers to any questions you might have.