Effective maintenance tracking lets you know if maintenance work is done on time and within budget. However, different teams have different requirements. It can be tricky to decide which features you need in your maintenance tracking software.
In this article, we’ll explore what maintenance tracking typically covers. We will also look at different software options — from CMMS and specialized scheduling tools like Sockeye to simple Excel and Outlook setups — to help you decide what’s best for your team.
What does maintenance tracking involve?
At its core, maintenance tracking is about following the progress of equipment maintenance work. This includes keeping tabs on preventive maintenance schedules and the execution of orders to make sure everything gets done when it needs to. It’s about knowing what’s due, what’s overdue, what’s completed, and what’s left in the backlog.
But maintenance tracking can mean a lot more than just tracking WOs and PMs. In a broader sense, maintenance teams might want to track other types of information to improve efficiency and reduce costs, including:
- Maintenance history: Documenting past repairs and inspections to spot recurring problems or identify equipment trends.
- Parts inventory: Tracking spare parts and supplies to avoid stockouts and prolonged downtime.
- Maintenance costs: Monitoring expenses related to labor, parts, and downtime, helping to keep budgets under control.
- Asset performance: Tracking equipment performance and condition to spot potential issues early and prevent failures.
With this in mind, let’s overview different types of maintenance tracking software — and see what you can track with them.
The main types of maintenance tracking software
Maintenance tracking software helps you organize, monitor, and manage your equipment maintenance schedules and work. Which one you should use depends on your goals and the maturity of your maintenance department.
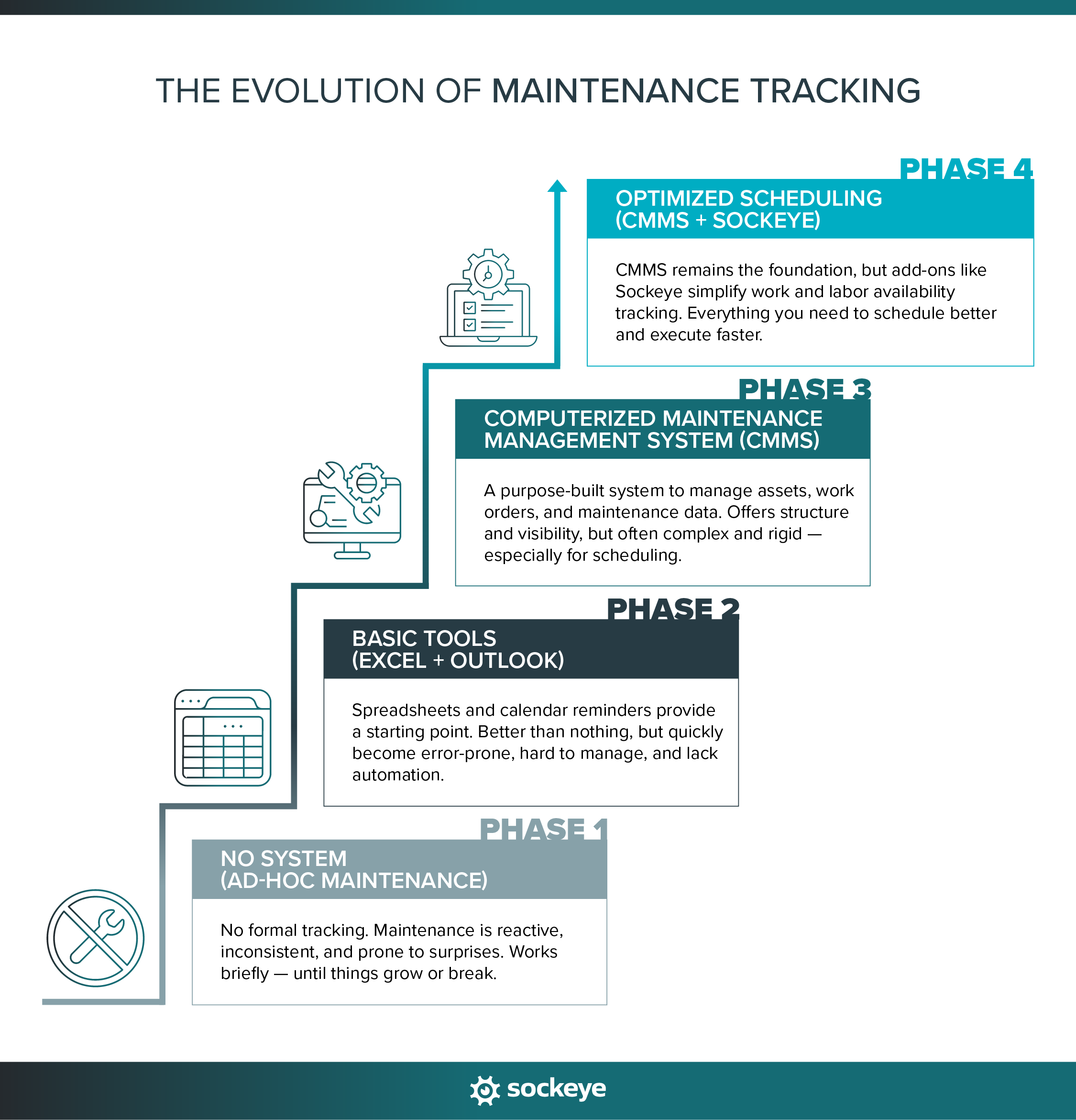
Many maintenance teams, especially small ones, start by not tracking anything formally. But that leads to inefficiencies and surprise breakdowns as soon as the team or the workload starts growing.
This helps them realize the value of systemic maintenance tracking. If they are cost-conscious, which most maintenance teams are, they will first test basic tools like Excel spreadsheets and Outlook calendars. While that is definitely better than nothing, it’s not a long-term solution.
As their maintenance database grows or their operations continue to scale, data inaccuracies and inefficiencies become too big to ignore. So, they eventually upgrade to a CMMS to streamline operations further. Learn more about this in our CMMS vs Excel debate.
Since there are hundreds of different CMMS providers, experiences will vary. Many teams find that their chosen CMMS is a good overall investment but has one major flaw — it makes work order scheduling and tracking way more complicated than it needs to be. They solve that problem by integrating a specialized scheduling add-on with their existing CMMS software.
In the following subsections, we’ll explore these software options in more detail to help you understand their strengths and limitations.
Excel spreadsheets plus Outlook
The easiest way to start tracking equipment maintenance is to use simple tools you already have, such as Excel and Outlook.
In this basic setup, Excel is usually used for recording backlogs, creating asset inventory lists, and leveraging templates to create and track maintenance schedules. Outlook calendars complement Excel by providing reminders and notifications about upcoming maintenance work or due dates.
However, relying exclusively on Excel and Outlook comes with several challenges:
- Limited scalability: As your maintenance workload grows, managing spreadsheets quickly becomes cumbersome and time-consuming.
- Prone to errors: Manual spreadsheet data entry increases the risk of mistakes, lost information, and outdated data.
- Poor visibility and collaboration: Spreadsheets are usually stored locally or in shared folders, making it hard for teams to collaborate, access the latest information, or get a clear picture of maintenance progress.
- No built-in tracking automation or reporting: You can use custom formulas and conditional formatting to highlight overdue tasks and have other basic tracking. However, it requires expertise and some trial and error to set everything up.
This approach can work for smaller maintenance teams managing a limited number of assets, where maintenance tasks are simple, infrequent, or easy to track manually.
Computerized Maintenance Management Systems (CMMS)
A Computerized Maintenance Management System (CMMS) is software specifically designed to help maintenance teams track, manage, and optimize their maintenance operations.
It is a big promise — and some vendors are much better at fulfilling it than others. The more capable solutions will help you track things like:
- Work order management: Automate scheduling and reminders for routine inspections or services. Track the status of maintenance tasks, assignment to team members, and completion history.
- Asset details and maintenance history: Keep organized records of past inspections, repairs, and issues for each asset. Some solutions might even enable you to track asset performance and condition over time.
- Parts inventory: Know exactly what spare parts you have in stock and when it’s time to reorder.
- Maintenance costs: Monitor spending to keep your maintenance budget under control and identify areas for savings.
While these solutions promise powerful features and significant benefits, they have their challenges. Many CMMS systems can be complex and challenging for maintenance teams to learn, adopt, and use effectively. Additionally, CMMS software often involves significant upfront costs, including training and setup, before you start seeing value.
Scheduling can also be limited in many CMMS solutions. Creating schedules and assigning work can still feel cumbersome or inefficient, often requiring additional scheduling tools.
Despite these obstacles, the benefits of using a CMMS typically outweigh the drawbacks — especially for teams looking to improve efficiency, reduce downtime, and make more informed maintenance decisions.
Scheduling add-ons like Sockeye
Scheduling add-ons, such as Sockeye, are simple tools designed to simplify work scheduling and tracking.
Rather than replacing your CMMS, these tools work alongside it to provide better visibility into technician availability, skills, and workloads. This enables you to quickly create effective schedules, as well as update them on the fly when unexpected issues arise.
We can’t know what other similar solutions do (and there aren’t many), so here’s what Sockeye helps you track:
- Backlog that is ready to go: Sockeye integrates with your CMMS to display ready-to-schedule work orders.
- Labor availability: We can pull the latest available technician and contractor hours from your HR systems. Don’t use one? No problem! You can manually input technician availability and shift patterns.
- Daily and weekly schedules: Simply select the work you want to schedule, and our automation will assign available technicians and contractors to build your daily/weekly schedule. The whole team can monitor work in progress and what has been completed.
- Crew utilization and overtime: Track the available hours you scheduled and see if you are running overtime. Use this to increase the amount of scheduled work each week without going into overtime.
- Work delays: Write notes explaining why specific work orders had to be delayed. Keep an eye on delayed work and accompanying notes to identify trends, find root causes, and take corrective actions.
- KPIs and metrics: Sockeye automatically tracks and reports on SMRP metrics (like schedule compliance) and provides a live KPI dashboard. You can also define and track custom KPIs.
The only drawback of these specialized solutions is that they don’t work great (or at all) as standalone solutions. But they can do wonders when combined with CMMS or EAM software.
Equipment maintenance tracking tips and best practices
Improving your equipment maintenance tracking doesn’t have to be complicated. Here are several practical tips and best practices to keep your maintenance operations running smoothly:
- Keep your data up-to-date: Accurate, timely data entry is crucial. Make it a daily habit to update maintenance tasks, work orders, and asset histories to avoid confusion and costly mistakes.
- Centralize your maintenance records: Store your maintenance data in one accessible place, whether that’s a digital folder, a CMMS or another specialized tool. Centralized data helps your whole team stay informed and work more effectively.
- Leverage automation: Use digital solutions to automate different aspects of your maintenance workflow. Automation reduces the risk of data loss and data entry errors.
- Regularly review maintenance metrics: Define and track maintenance KPIs that reflect your overall business goals. This helps you spot trends, identify problems early, and continuously improve your maintenance processes.
- Use visual scheduling tools: Visual weekly schedules make assigning and tracking work easier. Tools that show workloads, technician availability, and overdue tasks can help you respond proactively.
- Train your team: Make sure everyone understands how to use your maintenance software and follows data entry standards — like naming conventions, categorization methods, and required data fields to prevent errors and maintain data integrity.
- Simplify wherever possible: Choose software that’s easy for your team to learn and use. Overly complicated software leads to errors, low adoption, and wasted time.
Maintenance tracking should be simple
Tracking and reporting on equipment maintenance should simplify your job, not create hours of extra administrative work.
That’s why it’s crucial to choose solutions that are simple to learn, use, and navigate. The right maintenance tracking software should let your technicians spend less time at the computer or phone and more time doing what they do best — keeping equipment up and running.
Sockeye is designed precisely with this simplicity in mind. It helps your team do more work by smartly scheduling work and monitoring its progress.
Want to see how easy maintenance tracking can be? Schedule a demo of Sockeye today.