Industries such as manufacturing, healthcare, property management, and facility maintenance heavily rely on an effective work order system to keep their operations running smoothly. Whether it’s routine inspections or emergency repairs, having a reliable system in place makes all the difference.
To build such a system, you need standardized work order forms and tools that can help you efficiently schedule and manage work orders.
Continue reading to learn what should be included in a work order form and find ready-to-use templates to help you get started.
What is a maintenance work order?
A maintenance work order is a paper or digital form that outlines the maintenance work to be performed. It provides essential details about the job, such as the scope of work, materials needed, assigned personnel, and deadlines. Work orders help ensure that maintenance activities are properly tracked, prioritized, and completed.
The process usually starts with a work order request, which is submitted by a team member or stakeholder identifying an issue or needed service. Once reviewed and approved, the request is transformed into a formal work order with specific details to guide the maintenance team.
Maintenance work orders can be categorized depending on the type of work they cover. There isn’t an official list to follow, so here are the most common types we have seen used:
- Preventive Maintenance Work Order: Scheduled tasks to prevent equipment failures and prolong lifespan.
- Corrective Maintenance Work Order: Issued when an asset needs repair due to a detected issue.
- Emergency Work Order: Addresses urgent issues that require immediate attention.
- Inspection Work Order: Used for routine inspections to ensure equipment is in good condition.
- Routine Maintenance Work Order: Covers simple upkeep tasks such as cleaning and lubrication.
Despite this categorization, most, if not all, of the maintenance work can be issued using a single, standardized maintenance work order form. And one way to track the type of work performed is to include the Work Order Type field in your maintenance WO forms.
What should a maintenance work order form include?
A well-designed maintenance work order form captures all of the information technicians need to smoothly execute the assigned work.
Recommended items to include:
- Work order number: A unique identifier for tracking purposes.
- Work order description: A clear and concise explanation of the task to be performed.
- Priority level: Indicates the urgency of the task.
- Work order status: To track whether the WO is scheduled, in progress, or completed.
- Asset details: Information about the asset requiring maintenance (location, asset ID, etc.).
- Assigned personnel: The qualified team (i.e. electricians/pipefitters/welders…), shift, or individual responsible for completing the work.
- Labor required: An estimated number of people and total hours needed to perform the work.
- Estimated completion date: The expected timeline for task completion.
Optional items to include:
- Requestor information: Name and contact details of the person submitting the work request. This will be a useful field to have for field service teams.
- Materials required: List of materials or parts needed for the job.
- Labor costs: Estimated or actual costs related to labor.
- Notes/Comments: Additional information that provides more context and might be useful.
- Photos or attachments: Added to digital maintenance work order forms. Includes supporting images or documents like OEM manuals, troubleshooting diagrams, or SOPs.
- Safety procedures: Specific safety protocols to be followed during the task.
- Approval signatures: Authorization from relevant stakeholders.
Including these elements helps streamline the process for maintenance technicians. It also provides you with plenty of information to track different maintenance KPIs.
For reference, the images below show the info we include in the Sockeye maintenance scheduler. Of course, these fields are not set in stone and can be adjusted based on what your team needs.
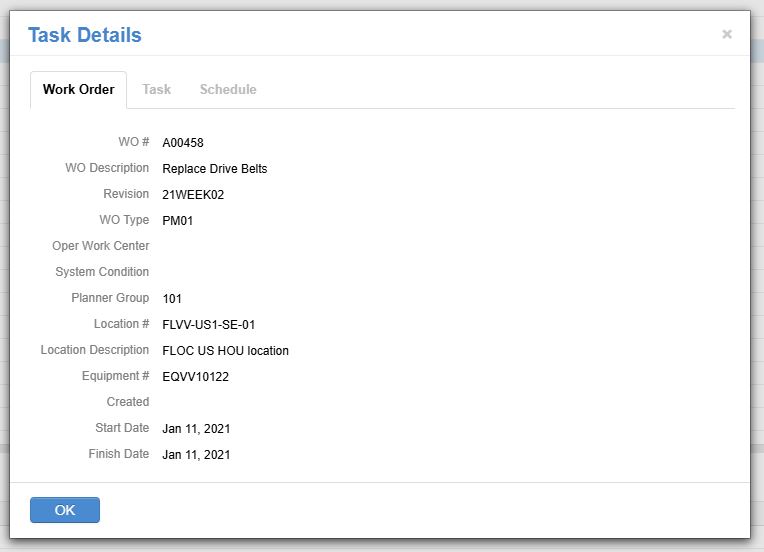
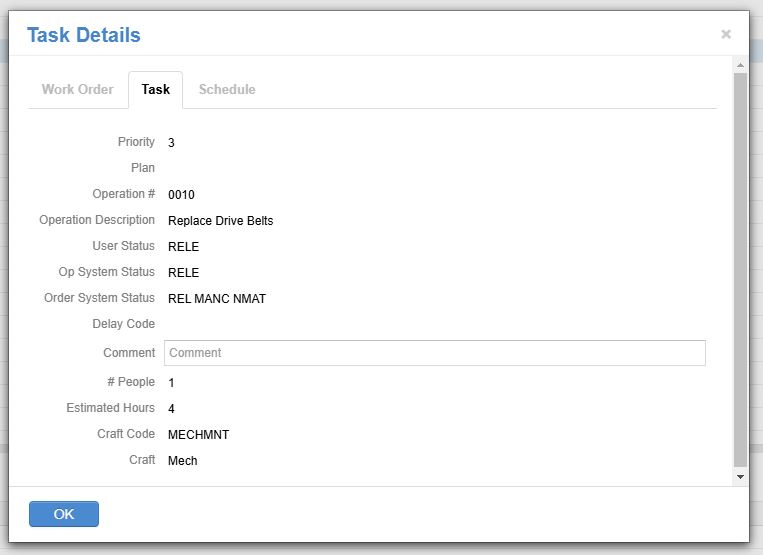
Maintenance work order templates
Standardized work order form templates help maintenance teams stay organized and efficient. Below are two ready-to-use templates that you can further customize to suit your specific needs.
Work order form template #1
This template provides a simple and structured format to assign maintenance work.
- Simple maintenance work order form template [GOOGLE DOCS]
- Simple maintenance work order form template [MS WORD]
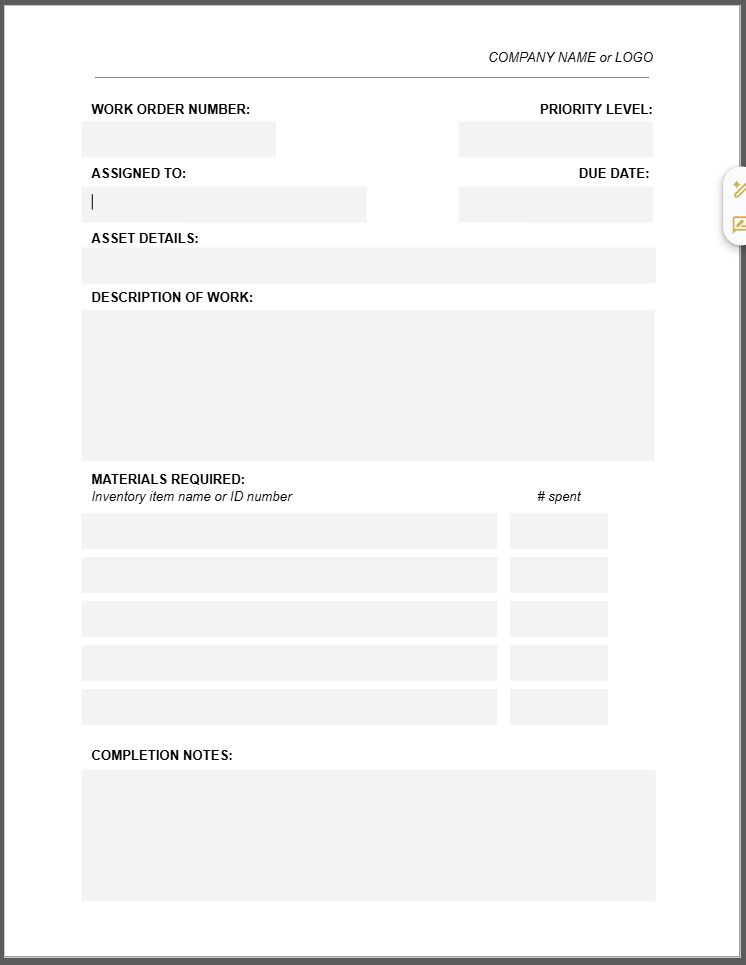
This template is ideal for in-house maintenance teams that need a straightforward template with only the essential fields.
After making a copy or downloading the document, you can adjust the templates to your needs. The document can be filled out on your computer before sharing it with your team — but it will work better if you print it out first.
Work order form template #2
A more detailed work order form template with additional fields for tracking costs, materials, and labor efforts.
- Advanced work order form template [GOOGLE SHEETS]
- Advanced work order form template [MS EXCEL]
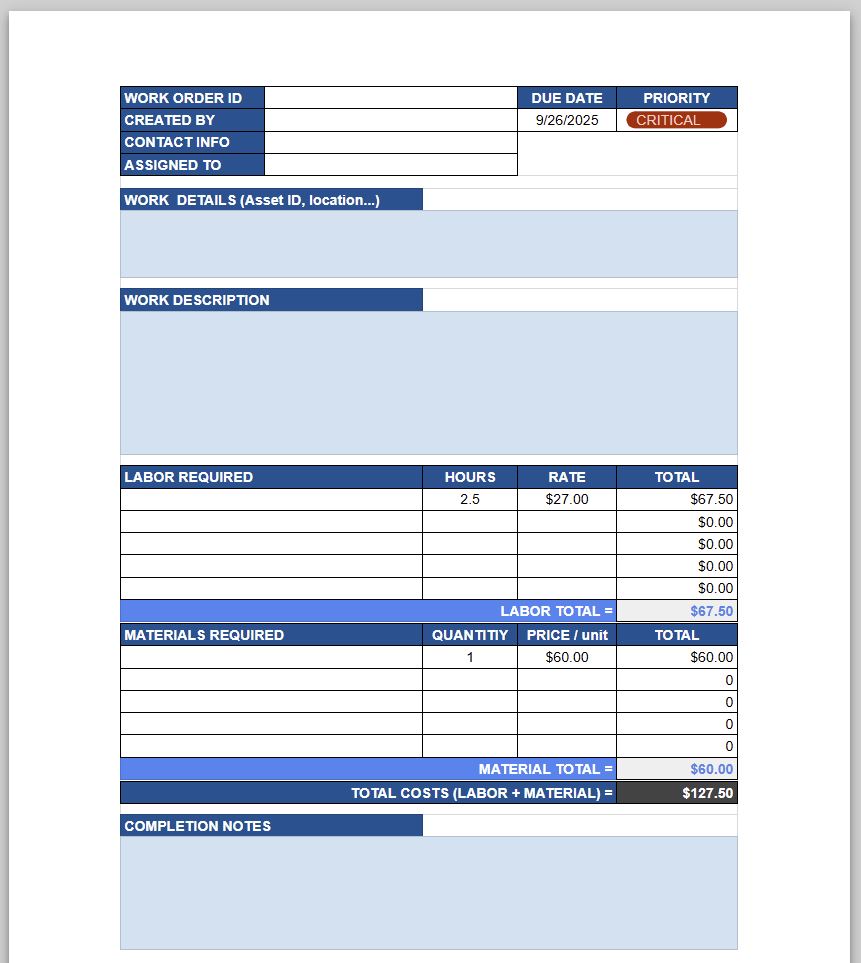
Great for teams that require more comprehensive tracking, including things like cost analysis. The template is created in Google Sheets and can be easily printed out. Again, after making a copy, you can tweak it to better suit your operational needs.
Streamline WO scheduling with Sockeye
Sockeye is a simple maintenance scheduler that simplifies work order scheduling and tracking. It functions as a CMMS bolt-on, meaning that it integrates with your existing CMMS software.
We have seen so many organizations that have a CMMS but still use Excel to schedule maintenance work — mainly because they find the scheduling function inside their CMMS too rigid or complex.
Sockeye is the perfect solution for those types of businesses. You can still use CMMS for everything else, but handle maintenance scheduling through Sockeye. Here’s a 90-second video that showcases how Sockeye works.
You need to schedule more work to get more work done. And Sockeye helps you do just that.
Jump on a quick call with our team to learn how Sockeye can simplify work order scheduling for your team.