Schedulers in busy manufacturing plants often juggle too much at once — trying to coordinate tasks, people, and machines — while also reacting to breakdowns and last-minute changes.
To make things work, manufacturers need a simple yet flexible scheduling tool — something that helps them stay organized, adapt schedules quickly, and make the most of their existing labor resources.
This is exactly the purpose for which Sockeye is built. Let’s see how you can combine it with any CMMS to create the ideal manufacturing maintenance scheduling solution.
Is CMMS good enough?
Many manufacturing plants already use a Computerized Maintenance Management System (CMMS) to organize maintenance work. It’s great for keeping records, tracking assets and parts inventory, and managing work orders. In many ways, it simplifies maintenance management by putting all your data in one place.
But when it comes to actual scheduling, most CMMS platforms just don’t cut it.
Modern CMMS solutions are often overloaded with features you’ll never use. The interfaces are cluttered, the workflows are rigid, and setting up a schedule can feel like solving a puzzle. On the flip side, older legacy systems are too inflexible — you have to follow their process, whether it works for your team or not.
Worst of all? Most CMMS tools don’t show real-time labor availability. So you end up assigning tasks without knowing if your technicians are even free. That’s how maintenance work gets delayed or scrapped, leading to prolonged downtime and production delays.
Because of these issues, a lot of teams end up falling back on Excel to build their schedules. And while spreadsheets offer more flexibility, they come with their own headaches — version control, human error, and inaccurate reporting, just to mention a few.
But there’s a better way. It’s called Sockeye.
Using Sockeye as your manufacturing maintenance scheduling software
Sockeye is a lightweight maintenance scheduling tool built specifically for maintenance teams in manufacturing.
It’s not a standalone solution — it bolts onto your existing CMMS or EAM software and handles only the scheduling part.
That focus on scheduling is exactly why it works so well. It’s simple, it’s visual, and it’s built around how maintenance actually happens on the plant floor.
Instead of wrestling with a bloated CMMS or trying to make Excel do things it wasn’t built for, you can use Sockeye to create, adjust, and share your equipment maintenance schedules in just a few clicks.
Here’s a 90-second overview of Sockeye:
Let’s take a closer look at its main features and why it works so well in a busy manufacturing environment.
Create weekly schedules in a couple of clicks
With Sockeye, building out your weekly (and daily) maintenance schedule is fast and intuitive.
You can leverage our built-in automation to generate a schedule based on real-time labor availability and technician skill sets. No more guessing who’s available or manually cross-checking calendars. Just select the tasks in your backlog and click the “Schedule” button — Sockeye does the rest.
Once the schedule is generated, you can make quick adjustments—drag, drop, or shift things around — and hit commit when it looks good. The schedule is instantly visible to everyone on the team, so there’s no confusion about who’s doing what and when.
It’s a huge time-saver and keeps everyone on the same page.
Boost production capacity with timely preventive maintenance
Preventive maintenance is essential — but it can be hard to fit in when production lines are always running and your team is stretched thin. We all know unplanned downtime is usually more expensive than scheduled maintenance, but squeezing it into the calendar is tough.
Sockeye helps you balance production and maintenance schedules, so you’re not constantly choosing between hitting output targets and maintaining your equipment.
With a clear view of labor availability and scheduled jobs, it is way easier to plan preventive tasks at the right time, without disrupting production. That means fewer breakdowns, better use of your workforce, and more equipment uptime overall.
Update maintenance schedules on the fly
Manufacturing plants are unpredictable. Equipment breaks, accidents happen, production plans shift, or new machines show up. It’s nonstop.
That’s why static schedules just don’t work.
With Sockeye, you can adjust your maintenance schedule on the fly — no need to scrap everything and start over. If a technician calls in sick or a critical machine goes down, you can quickly reschedule or reassign work to another crew or technician.
Most scheduling tools allow you to do that. The difference is that Sockeye makes it extremely simple — you just need to drag and drop the task to the next available slot. This way, rebalancing your daily and weekly workloads takes minutes, not hours.
This kind of flexibility is a game changer for keeping maintenance work on track in the real world.
Catch up on backlog by scheduling more work
Backlog is a common problem, especially in plants that perform a lot of reactive maintenance. It’s hard to get ahead when you’re constantly putting out fires.
Sockeye helps you flip the script.
Our tool is built around availability. If you have two electricians working 8 hours per day, you can schedule 16 hours of electrical work each day or 80 hours per week. Sockeye helps you load their schedules to at or near 100% of their availability.
By having a clear picture of who’s available and when, you can start fitting more planned work into the schedule — whether that’s preventive tasks, deferred jobs, or corrective maintenance that’s been sitting in the queue.
In other words, Sockeye helps you get more work done by smartly scheduling more work.
The result? You can finally make a deferred maintenance plan and start clearing out the backlog.
Track key scheduling metrics
If you want to improve maintenance scheduling, you need to know what’s working — and what’s not.
Sockeye gives you visibility into key SMRP scheduling metrics like:
- Percentage of scheduled work completed on time
- Labor utilization rates
- How much preventive vs reactive work have you been doing
- How much work has been spent on standing work orders and emergency work
- And much more.
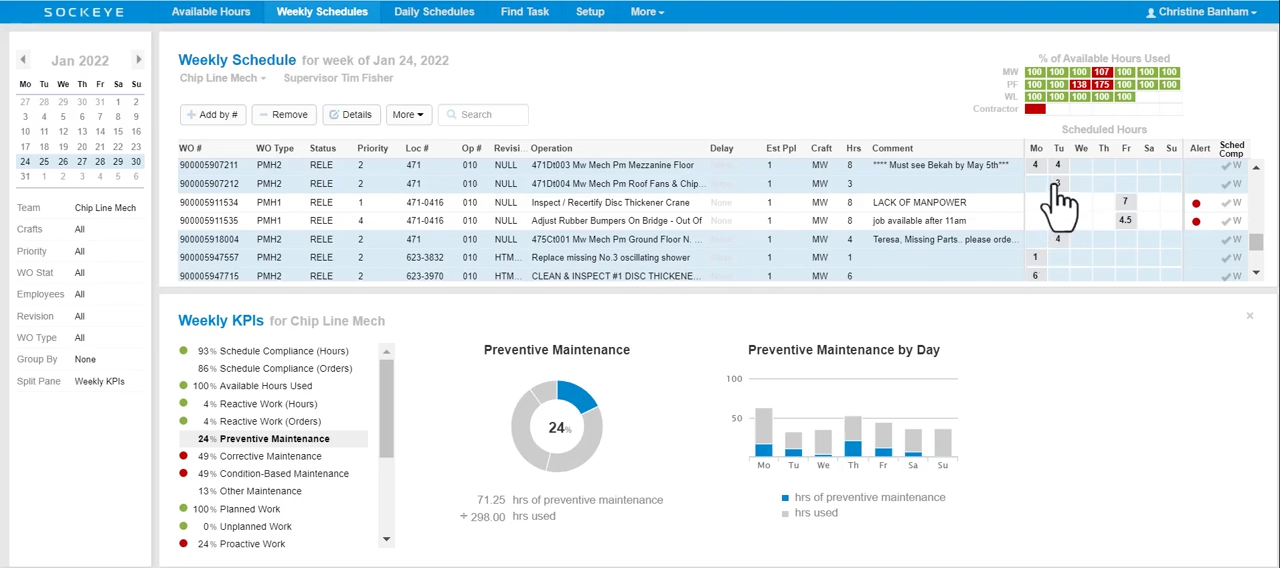
These insights help you spot patterns, uncover bottlenecks, and make smarter scheduling decisions moving forward.
It’s not just about building a better schedule today — it’s about optimizing every week after that.
How Sockeye boosts productivity at manufacturing plants
Sockeye worked with AV Group, which produces high-quality dissolving grade pulp used to manufacture viscose staple fiber, to streamline maintenance of their mill assets and ensure optimum production capacity.
They came to us while facing significant challenges in their maintenance scheduling processes. Relying heavily on spreadsheets, the team encountered issues with data fragility, labor-intensive workflows, and unreliable KPIs.
Our support team ensured the transition to Sockeye was smooth. After streamlining their scheduling processes with Sockeye, they have seen improvements almost immediately:
- Time efficiency: The effort to create a shutdown schedule was reduced dramatically, saving valuable planner time.
- Cost savings: Enhanced visibility into labor allocation allowed for better resource leveling between crews, significantly reducing their overtime expenses.
- Better data integrity: With direct synchronization from their CMMS, the reliability of scheduling data improved, fostering greater trust in the metrics used for decision-making.
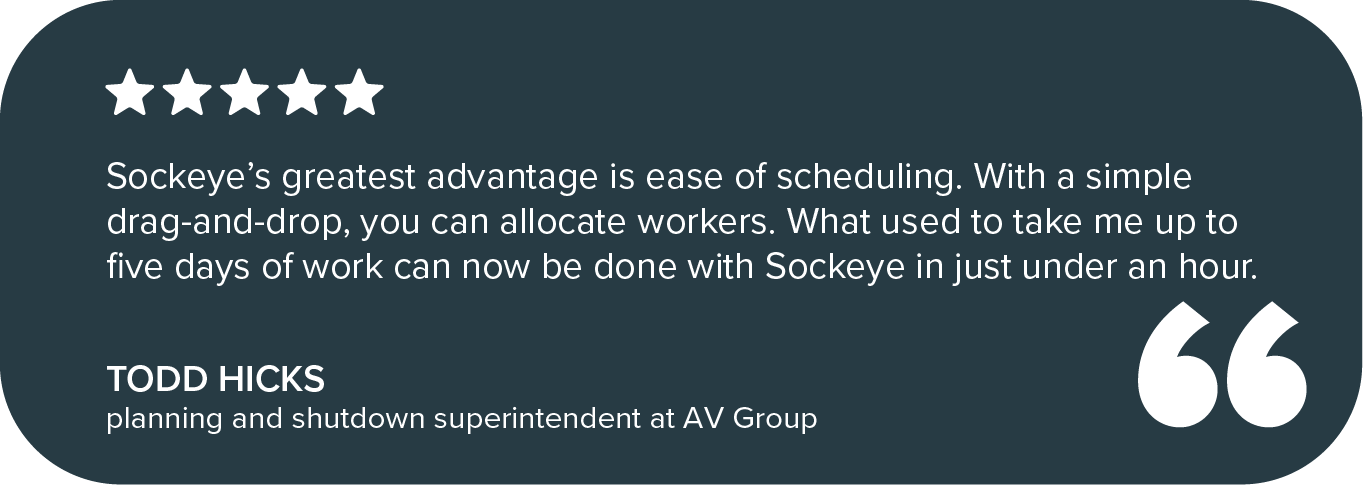
Overall, Sockeye’s implementation at AV Group resulted in optimized scheduling accuracy, reduced operational costs, and improved confidence in mill-wide metrics, contributing to enhanced production uptime and capacity.
Simplify plant maintenance scheduling with CMMS and Sockeye
CMMS systems are great at organizing maintenance data — but they’re rarely built for fast, flexible scheduling. That’s where Sockeye fills the gap.
By plugging Sockeye into your existing CMMS, you get a powerful, visual scheduling tool that’s easy to use, adapts to change, and helps your team stay on track — without the complexity of traditional solutions or the chaos of spreadsheets.
Best part? You don’t have to commit right away.
Sockeye offers a free trial, so you can test it out with your own data, your own team, and your actual maintenance process. Setup is quick, with no IT resources needed; we only ask for a copy of your schedule and one hour of your time.
Schedule a quick demo with our team, and we’ll show you how Sockeye can simplify your plant’s maintenance scheduling!