A preventive maintenance schedule is a detailed plan that outlines when and what type of maintenance work should be performed on your assets to keep them in optimal condition. It’s all about being proactive — addressing potential issues before they become expensive problems.
The purpose of a PM schedule is to ensure that nothing slips through the cracks. It can include everything from routine inspections and lubrication to part replacements and system checks. A good PM schedule minimizes downtime, extends equipment life, and ultimately saves time and money.
In this guide, we’re breaking down the process of creating a preventive maintenance schedule into simple, actionable steps. We’ll explore the different types of PM schedules you can run, provide a step-by-step process for building one, and share some examples to get you started.
Let’s dive in!
Types of PM schedules to choose from
Preventive maintenance schedules generally fall into two main categories: usage-based and time-based. Both are designed to keep your equipment running smoothly by addressing issues before they escalate into costly breakdowns.
While there are other maintenance strategies out there — like condition-based and predictive maintenance — we will concentrate on the two mentioned above as they are more common and easier to implement.
Let’s quickly check the differences between usage-based and time-based schedules to help you choose the right approach for your equipment.
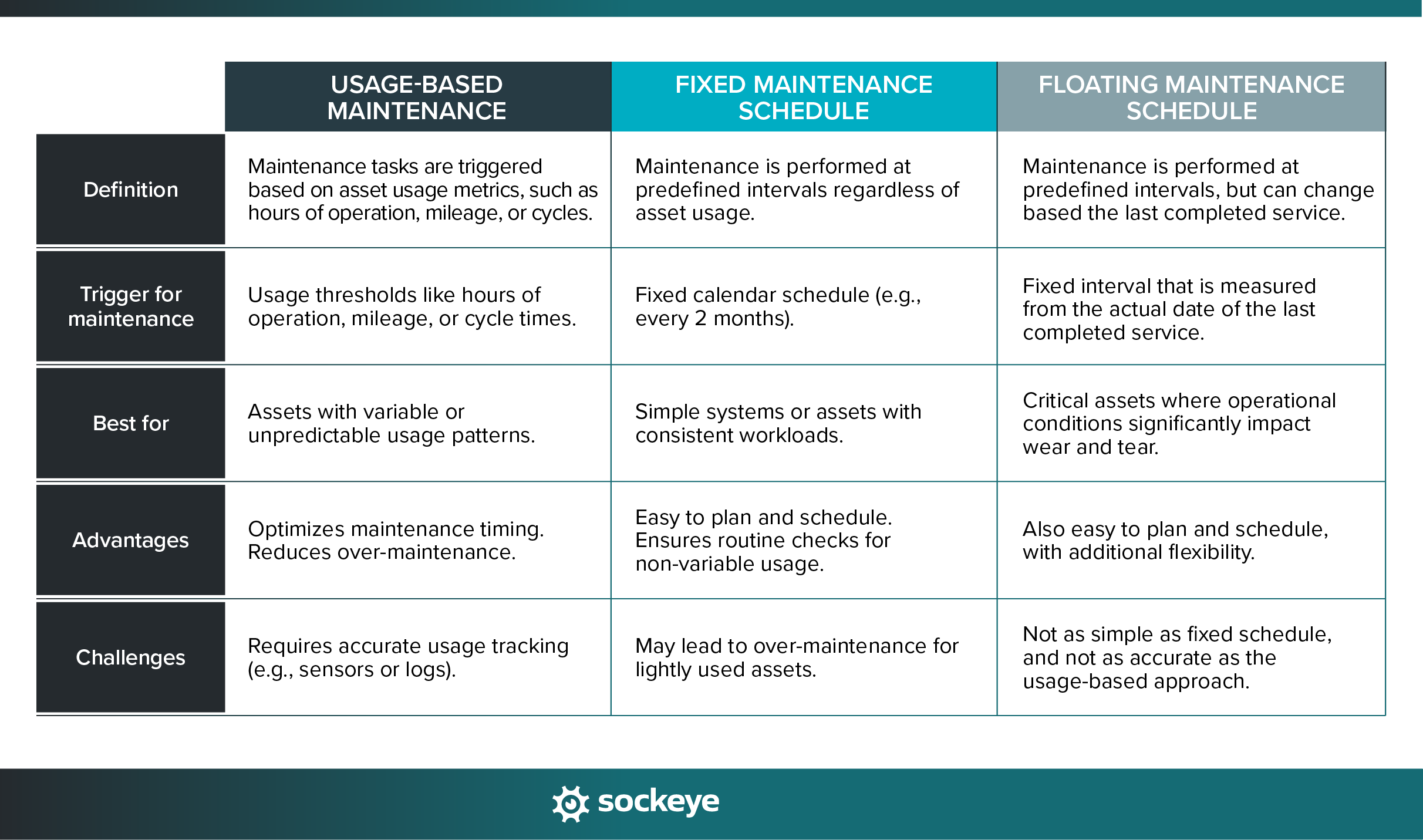
1) Usage-based maintenance schedule
A usage-based maintenance schedule (a.k.a. meter-based maintenance) triggers maintenance tasks based on how much an asset is used. Instead of relying on calendar dates, this approach looks at metrics like runtime hours, production cycles, or mileage. For example, a vehicle might require an oil change every 5,000 miles, or a generator might need servicing after 1,000 hours of operation.
Pros of usage-based maintenance:
- Tailored to actual usage: Maintenance volume more closely reflects the actual needs of the equipment, reducing unnecessary work and saving resources.
- Better equipment performance: Since tasks are based on real-world usage, equipment is less likely to experience wear and tear from over- or under-maintenance.
- Ideal for high-use assets: Particularly useful for equipment that operates under variable workloads.
Challenges of usage-based maintenance:
- Monitoring required: Accurate data collection on usage metrics is crucial, which may require additional tools or software.
- Inconsistent schedules: Maintenance intervals can vary, making it harder to predict workload or plan resources.
This type of schedule is a great fit for facilities with equipment that sees fluctuating demand. By focusing maintenance efforts where they’re needed most, usage-based schedules can improve reliability while reducing downtime.
2) Time-based maintenance schedule
A time-based maintenance schedule (a.k.a. calendar-based maintenance) focuses on performing maintenance tasks at regular, predefined intervals — regardless of how much the equipment has been used. This can be weekly, monthly, quarterly, or annually. Time-based schedules can be further divided into fixed and floating schedules to better suit operational needs.
In a fixed time-based schedule, tasks are performed on predetermined calendar dates, even if the previous service didn’t occur as planned. For example, if maintenance for a generator is scheduled every three months on January 1st, April 1st, etc., the schedule does not shift — even if a January service is delayed to February. The next maintenance would still be due on April 1st, keeping the original timeline intact.
In a floating time-based schedule, the maintenance interval starts from the actual date of the last completed service. For example, if a generator is due for maintenance on January 1st, but the service is delayed to February 1st, the next maintenance would be scheduled three months later — on May 1st. This approach adjusts the schedule dynamically based on actual completion dates.
Pros of time-based maintenance:
- More predictable planning: Easy to implement and plan for, making resource allocation simpler.
- Consistent execution: Ensures maintenance is performed regularly, which is particularly beneficial for assets that degrade over time.
- No usage monitoring needed: Suitable for equipment where usage data is hard to track or irrelevant.
Cons of time-based maintenance:
- Potential for over-maintenance: Tasks may be performed unnecessarily if the equipment hasn’t been heavily used.
- Less flexibility: Fixed intervals may not account for changes in workload or operating conditions.
- Resource intensive: Regular schedules might strain resources during peak seasons.
Time-based maintenance is a straightforward and reliable approach, particularly for assets that experience steady wear or operate under predictable conditions. It’s also a great choice for companies looking for a simple method to maintain compliance with industry standards or regulations.
How to create a preventive maintenance schedule
Preventive maintenance is a cornerstone strategy for many facilities; in fact, 88% of industrial facilities follow a preventive maintenance approach. However, many of them struggle to consistently create weekly schedules — and stick to them.
It’s one of the reasons why focus should be on establishing a clear, structured, and realistic plan.
In this section, we’ll walk through six straightforward steps to build your own preventive maintenance schedule.
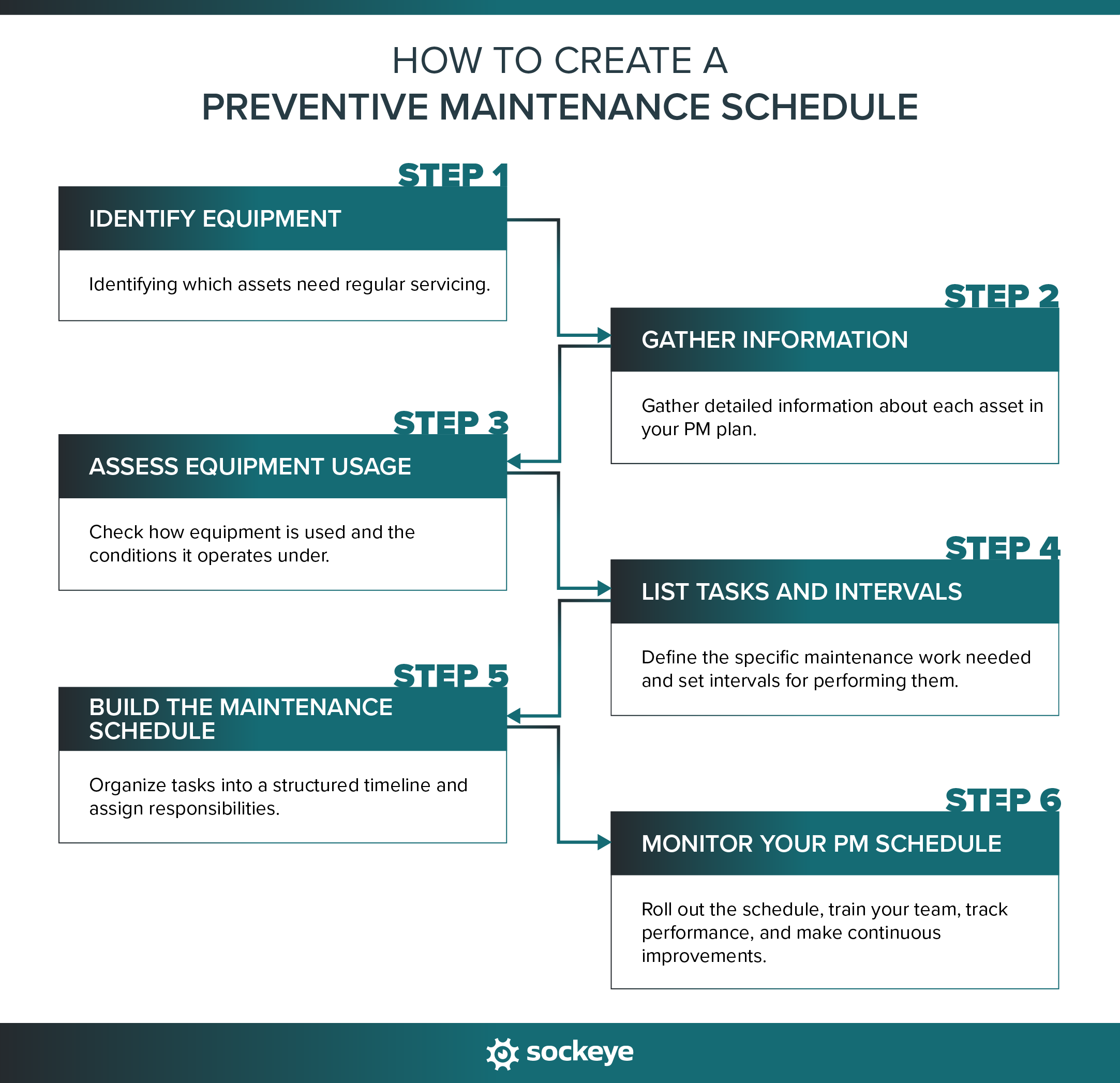
Step #1: Identify equipment that requires regular maintenance
The first step in creating a preventive maintenance schedule is identifying which assets need regular servicing.
If you do not have a centralized “database”, you should create an inventory list of all the equipment, machines, and systems in your facility. Document all equipment, including details like make, model, serial numbers, and current condition. Use a CMMS/EAM or a spreadsheet to simplify this process.
After that, you’ll want to categorize equipment — group assets based on the potential impact of their failure on operation. For example:
- High-criticality: Machinery that is very expensive to repair and/or essential to production, like a conveyor belt in a manufacturing line.
- Medium-criticality: Assets that support operations but don’t stop production if they fail, like a forklift or a secondary compressor that supports operations during peak times.
- Low-criticality: Non-critical systems like office HVAC units.
This foundational step sets the stage for a well-organized and effective PM schedule.
Step #2: Gather information about those assets
Once you’ve identified the equipment that requires regular maintenance, the next step is to gather detailed information about each asset. You’ll need this data to develop tailored maintenance tasks and intervals for each asset.
You can do the following:
- Review equipment manuals: Manufacturer manuals are invaluable resources. They often include recommended maintenance tasks, intervals, and critical safety information.
- Analyze historical data: Does a piece of equipment fail more frequently under certain conditions? Were there any missed maintenance intervals that led to unplanned downtime? Review past maintenance records to identify trends, common issues, and the actual performance and condition of the asset over time.
- Consult with operators and technicians: Frontline workers often have firsthand insights into how equipment performs and what issues they’ve encountered. Their input can uncover overlooked maintenance needs.
For example, the manual might recommend changing your HVAC filter every three months. However, historical data could show that filters clog faster during summer, suggesting the need for more frequent replacements during warmer periods. By combining manual guidelines and real-world insights, you can refine your maintenance schedule.
Step #3: Assess equipment usage and operating conditions
Understanding how your equipment is used and the conditions it operates under is critical to setting realistic maintenance intervals. Different assets experience wear and tear at varying rates depending on factors like:
- Operational hours: Measure how long the equipment runs during a typical day, week, or month. For example, a production line conveyor operating 24/7 will require more frequent maintenance than one used sporadically.
- Workload: Consider the intensity of the equipment’s operation. Heavy workloads can lead to faster wear and tear, demanding more frequent upkeep.
- Environmental conditions: Factor in the surrounding environment. For instance, equipment operating in a dusty or corrosive environment may need more frequent cleaning and lubrication. Similarly, outdoor equipment exposed to weather extremes will likely require regular inspections for rust or damage.
Skipping this step can lead to under-maintenance (causing premature failures) or over-maintenance (wasting resources). Performing due diligence allows you to tailor the preventative maintenance schedule to real-world operating conditions.
Step #4: Develop maintenance tasks and intervals
At this point, you should have the necessary information to define the specific maintenance work and set intervals for performing them.
First, you should outline the maintenance work that needs to be done. Identify the activities required for each asset, such as inspections, cleaning, lubrication, part replacements, or recalibration.
Then comes the challenging part — setting realistic maintenance intervals. Base intervals on criticality, usage, and risk of failure. Consider working with your reliability manager and performing FMEA or equipment criticality analysis. This should help prioritize work and set appropriate intervals.
And remember, while doing excessive maintenance is something you should watch out for, we mirror the sentiment Paul Lachance expressed in his article over on Plant Engineering:
“Can you schedule too many PMs? Yes you can. Still, too many PMs are probably better than not enough.”
Step #5: Build the maintenance schedule
With your maintenance tasks and intervals established, it’s time to build the actual PM schedule. This step involves organizing tasks into a structured timeline and assigning responsibilities.
For more actionable insights and best practices, check out our detailed guide on maintenance scheduling.Keep in mind that the process is going to be much easier when supported by maintenance software. For example, with the right information available, a maintenance scheduling app like Sockeye can automate steps of the scheduling process. Here’s a quick overview of how it helps schedule and manage both preventive and reactive work:
With the right tools and structure in place, your schedule will become a reliable framework for keeping operations running smoothly.
Step #6: Implement and monitor your PM schedule
Creating a preventive maintenance schedule is only half the battle — successful implementation and ongoing monitoring ensure it delivers results. You’ll need to roll out the schedule, train your team, track performance, and make continuous improvements.
If you’re doing this for the first time, start with a pilot project or phased implementation:
- For a large operation, test the schedule with a subset of equipment or a specific department. This allows you to refine the process before a full-scale rollout.
- For smaller operations, begin with high-priority assets and gradually expand to less critical equipment.
Again, you can use tools like CMMS and Sockeye to track your KPIs and whether work is being completed on schedule.
Based on the incoming data, you can make targeted improvements to your schedule. You’ll end up with a dynamic and reliable system that evolves with your operation’s needs.
Preventive maintenance schedule example
We went through a lot of theory, so let’s look at a few examples as well.
Sample PM schedule
To bring the steps to life, here’s a sample preventive maintenance schedule for a manufacturing facility focused on maintaining three critical assets: a conveyor belt system, an HVAC unit, and an air compressor.
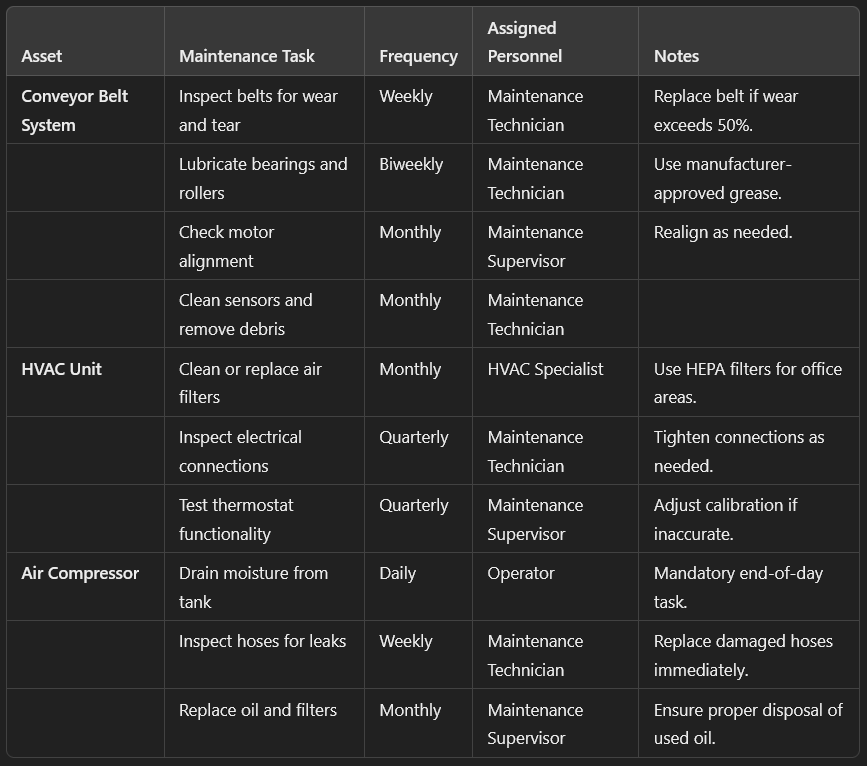
Key takeaways from the example:
- Tasks are clearly defined and matched to equipment.
- Frequencies are tailored to asset usage and criticality.
- Roles and responsibilities are assigned to ensure accountability.
- Notes provide additional clarity for special conditions or instructions.
This is a simple format that can serve as a great starting point. Depending on your industry, facility, and assets, your schedule may look significantly different.
The role of a preventive maintenance calendar in PM scheduling
A preventive maintenance calendar helps visualize all the tasks in your PM schedule. It provides a quick overview of what needs to be done, when, and by whom. Here is an example of a weekly schedule maintenance calendar from Sockeye. You can see the list of scheduled tasks, backlog, breakdown of work by days, the percentage of available hours used, and more.

On the left, you see the calendar to know which week of the month and year you are looking at. You can also apply dozens of different filters to simplify managing a higher volume of maintenance work.
While it’s not mandatory to have one, most maintenance teams will agree that a maintenance calendar is a useful tool that helps them stay organized.
Use Sockeye to take out complexity from preventive maintenance scheduling
Managing a preventive maintenance schedule can be challenging, especially as operations grow and assets increase in number and complexity. This is where Sockeye comes in — software designed to simplify and optimize your maintenance scheduling processes.
It does that through:
- Automated scheduling: Sockeye eliminates the manual effort of tracking due dates and assigning tasks. It can generate weekly schedules automatically using predefined criteria. You can then adjust them and build daily schedules based on your needs.
- Centralized task management: All your maintenance tasks are stored in one platform, making it easy to track progress and ensure accountability.
- Visual overview: Sockeye’s calendar lets you visualize scheduled tasks and available hours at a glance. This helps you set and adjust schedules with ease, and quickly respond to changes in operations.
- Advanced reporting and analytics: Gain insights into schedule compliance and other KPIs to track performance and make data-driven optimizations.
- Seamless integration: Sockeye integrates with your existing spreadsheets, CMMS, or asset management systems. If you’re unsatisfied with how your CMMS/EAM handles scheduling, you can simply connect it with Sockeye and use our intuitive scheduling interface instead.
Ready to see it in action? Schedule a demo and discover how Sockeye removes complexity from the scheduling process!