When it comes to keeping equipment running, maintenance teams often find themselves stuck between putting out fires and trying to prevent them in the first place. You’ve probably heard that reactive maintenance is bad and preventive maintenance is good — but the truth is a bit more nuanced.
Today, we’ll break down what each approach involves, how they stack up against each other, and why combining both (in the right way) might just be the most effective strategy.
Preventive vs reactive maintenance: A quick comparison
Reactive maintenance is what happens when something breaks — and then you fix it. It’s unplanned, often urgent, and usually disruptive. Common examples of reactive maintenance include:
- Fixing a conveyor belt after it stops working.
- Replacing a burned-out motor.
- Repairing a leaky pipe after it bursts.
Preventive maintenance, on the other hand, is all about staying ahead of problems. It’s scheduled work, often repeatedly, designed to keep equipment in good shape and reduce the chances of failure. For example:
- Lubricating machinery every 30 days.
- Replacing air filters every 3 months.
- Running regular inspections or calibration checks.
Below is a quick side-by-side comparison:
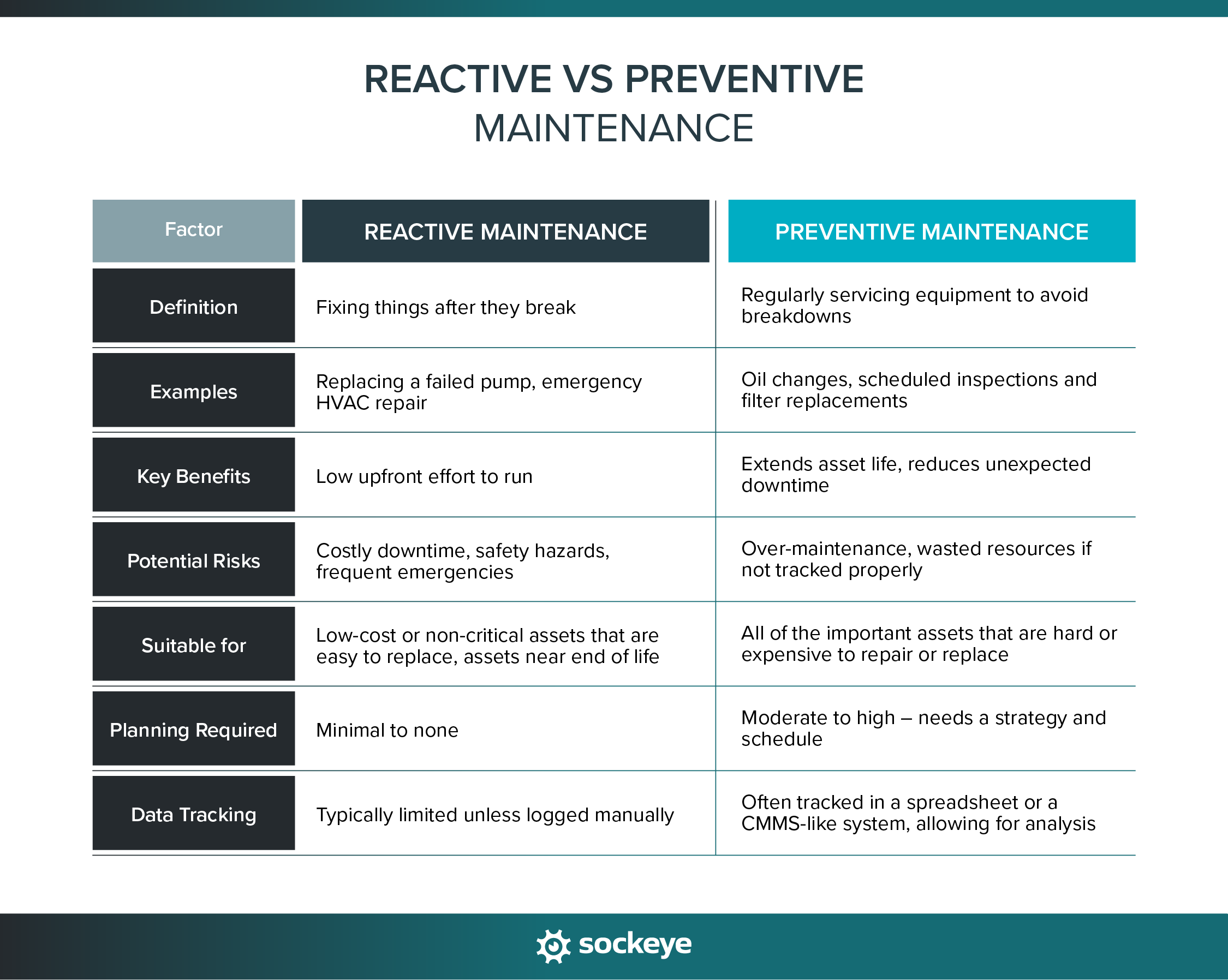
Reactive maintenance is not all bad
Reactive maintenance tends to get a bad rap — and for good reason. Relying too much on it can lead to unplanned downtime, costly repairs, safety risks, and frustrated production teams.
But here’s the thing: not all reactive work is a disaster.
The real problem is unplanned reactive maintenance. When something fails unexpectedly and there’s no backup plan, it can throw everything off. Production stops, technicians scramble, and costs start to pile up fast. That’s the type of reactive work most people are trying to avoid.
However, there’s a big difference between unplanned and strategically planned reactive work. In some cases, the best move is to let an asset run until it fails — especially if:
- The asset is cheap and easy to replace (and isn’t essential to day-to-day operations).
- The failure won’t cause safety or environmental issues.
- The asset is nearing the end of its useful life, so you already have a plan in place to replace it.
When used intentionally, run-to-failure maintenance can help teams avoid over-maintaining equipment and wasting time on unnecessary work. The key is knowing which assets can handle it — and being prepared for when they do go down.
Preventive maintenance is not all good
Preventive maintenance helps reduce unexpected breakdowns, improves safety, extends equipment life, and gives maintenance teams more control over their workload. It is also fairly simple to implement and run, making it the most popular maintenance strategy overall.
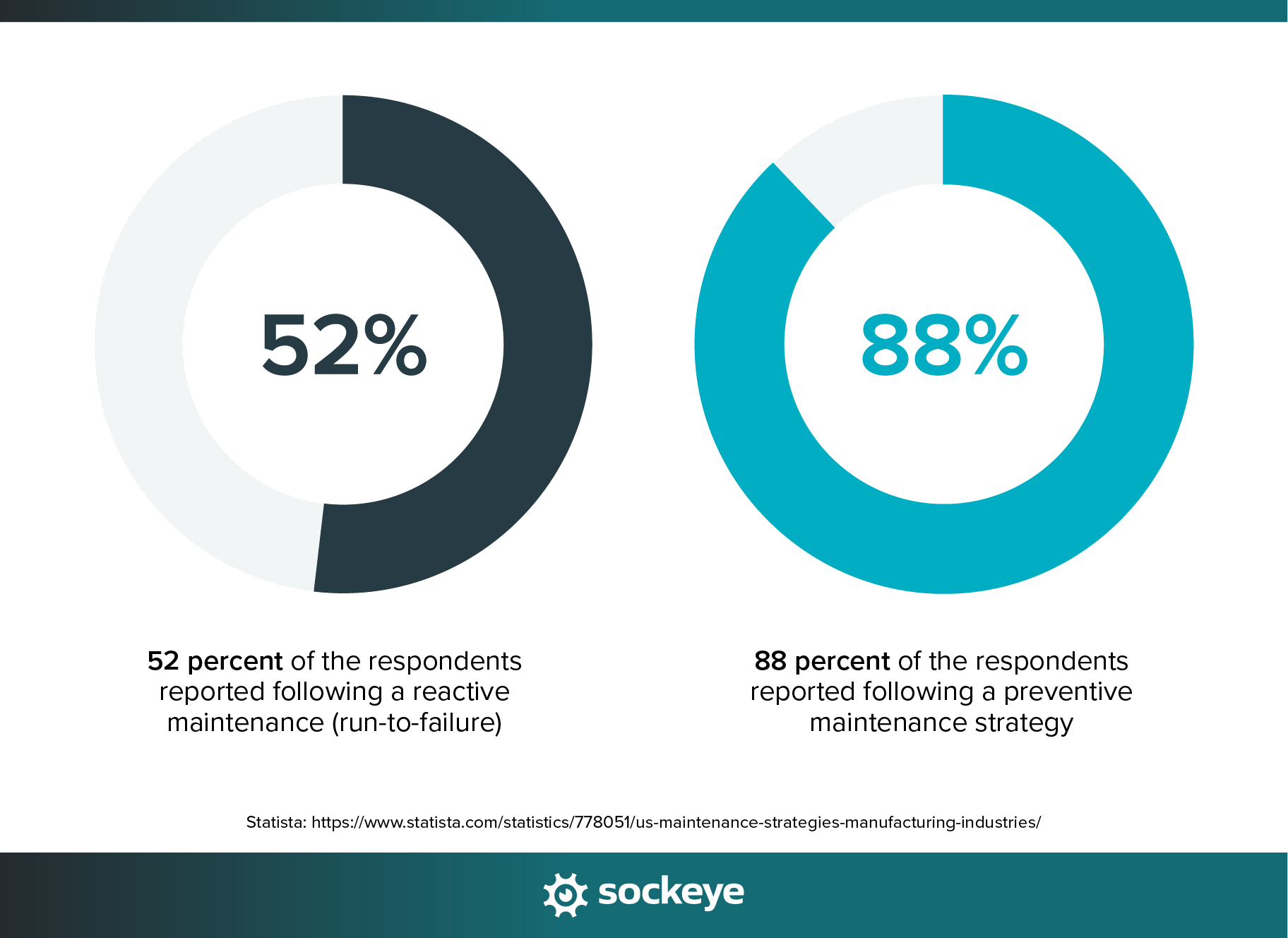
Here’s a complication: just because work is planned ahead doesn’t automatically mean it is an optimal move. In this case, there can actually be too much of a good thing.
Figuring out the exact volume of preventive work an asset might need can be tough. Do too little and the asset will fail; do too much and you are wasting your limited resources.
That’s why tracking the results of your preventive work is important. If equipment is breaking before the next scheduled service, it’s a signal to adjust your schedule and up the frequency of preventive work. Estimating when you might be doing too much maintenance is a little bit harder — it can include:
- Comparing MTBF before and after changing PM frequencies. If there’s no real change, consider scaling back.
- High maintenance schedule compliance should lead to fewer breakdowns. If it doesn’t, you may be doing PMs that aren’t targeting the real failure modes.
- Rating tasks based on whether they prevented a failure, detected an issue early, or resulted in “no issues found”. If an inspection routinely finds nothing wrong, it might be a candidate for rescheduling or elimination.
In short: preventive maintenance is powerful, but your maintenance schedules should be informed by good data (breakdown history, actual wear and performance data, etc.). Otherwise, you could end up doing “busy work” that doesn’t add much value.
How do you measure reactive maintenance vs preventive maintenance work?
Maintenance managers often ask us if Sockeye (our simple maintenance scheduler) can help them accurately track the volumes of reactive and preventive work done at their facility.
The answer is a resounding yes. Sockeye carefully tracks the time each of your preventive and corrective work orders take to complete — and automatically generates a report you can pull up at any time for a quick visual overview.
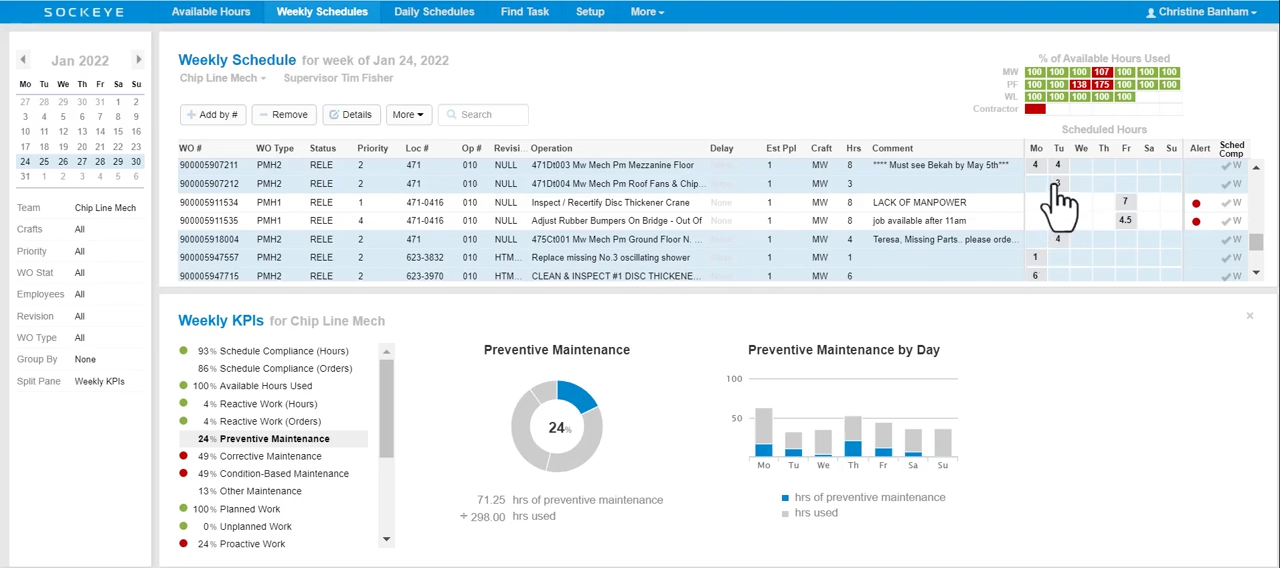
This helps you:
- Visualize trends: Are you spending more time fighting fires or preventing them?
- Set benchmarks: Want to reduce reactive work by 10% this quarter? You’ll have the data to measure progress.
- Spot resource drains: Certain assets might be consuming a lot of reactive time — a signal to increase preventive focus.
Without this kind of visibility, it’s almost impossible to improve. Tracking makes it clear when your efforts are working and when adjustments are needed.
How to make them work together
Preventive and reactive maintenance aren’t enemies — they’re just different tools for different jobs. The trick is knowing when to use each approach and on which assets.
Hopefully, this article provided some practical tips for simplifying this decision when planning future maintenance work.
You can also make your life easier by having the right systems in place. That’s where digital scheduling tools like Sockeye come in. It makes it easy to:
- Schedule both preventive and reactive work in the same system. In fact, with the workforce availability data, you will be able to schedule more work overall — meaning more PM and reactive work will get done each week.
- Reschedule work using our drag-and-drop functionality when emergencies or breakdowns happen.
- Level work between different crews to create a more balanced workload and reduce overtime hours.
- Track reactive vs preventive work, planned vs unplanned work, and much more.
- Publish a live, verified schedule that keeps everyone aligned — so technicians, contractors, planners and schedulers, and supervisors stay on the same page.
When the unexpected happens (and it will), Sockeye helps teams shift gears without losing track of everything else. That flexibility is key to managing a realistic, balanced maintenance schedule — one that quickly reacts to issues when needed but always keeps the bigger picture in view.