SAP is a powerhouse for enterprise resource planning (ERP) and offers a robust maintenance module to help organizations manage their maintenance operations. However, while SAP PM is incredibly feature-rich, many maintenance managers find it overwhelming when it comes to work order management and maintenance scheduling.
From creating notifications to scheduling and closing work orders, the process can be complex, rigid, and time-consuming.
Let’s check how SAP work order management works, why many find it complicated, and how you can use a simple bolt-on like Sockeye to streamline the process.
How work order management works inside SAP software
SAP offers a comprehensive maintenance module known as SAP Plant Maintenance (SAP PM). It facilitates the planning, scheduling, and execution of different maintenance tasks. One of the key features of this module is work order management — enabling the creation, planning, and tracking of maintenance work orders. Its functionality allows maintenance teams to document tasks, allocate resources, and monitor work progress.
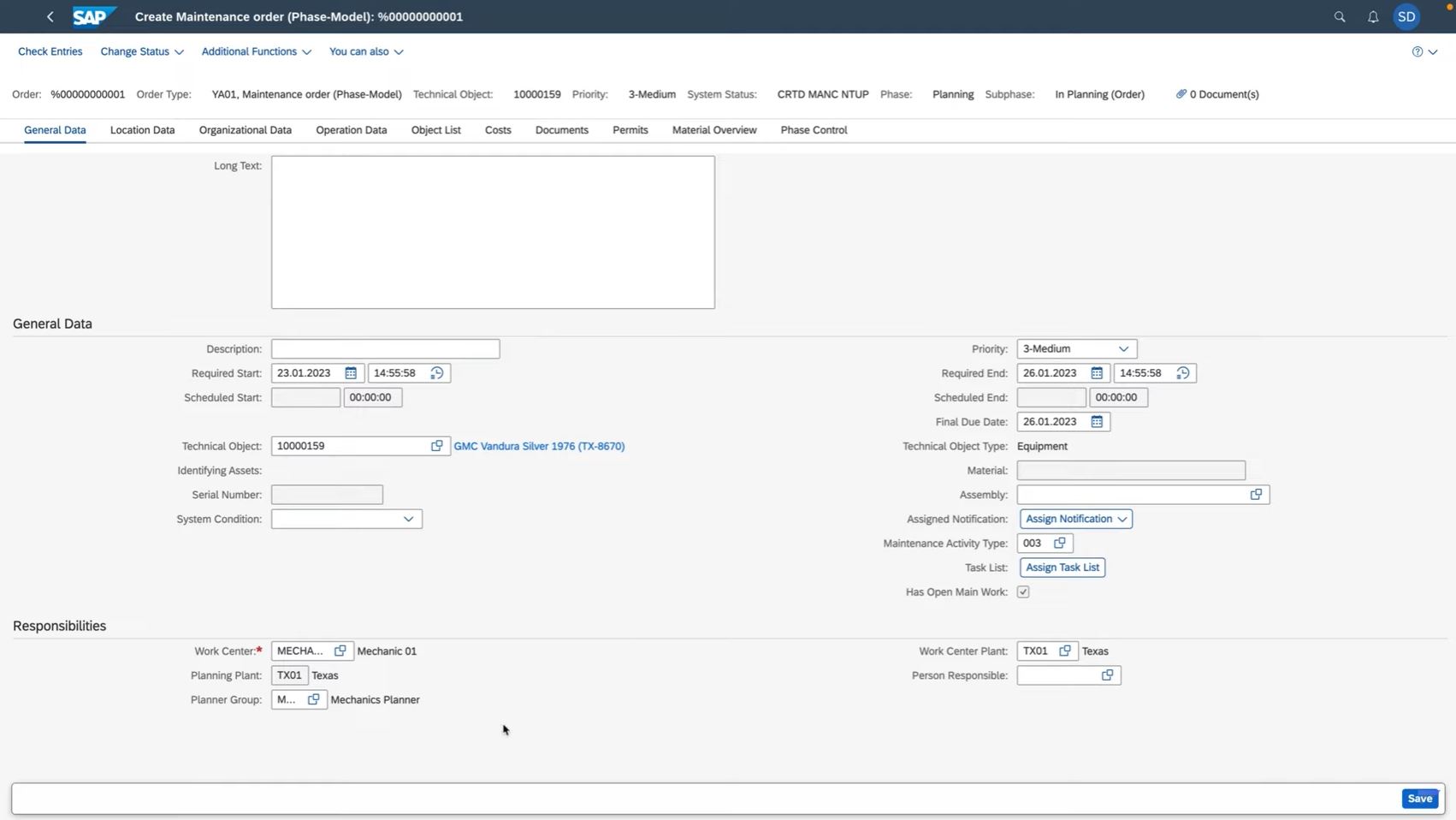
Screenshot of the first step of creating a WO in SAP.
SAP work order management follows the standard WO process:
- Notification creation: After a maintenance need or malfunction is identified, the maintenance planner creates a Maintenance Notification in SAP PM. They include details about the issue, such as equipment, location, and description of the work needed, and assign a priority to indicate its urgency.
- Work order creation: The planner converts the notification into a Work Order to begin the maintenance process. This step involves linking the notification to the work order and specifying the type of maintenance required, such as corrective, preventive, or emergency work.
- Work order planning: During planning, the planner organizes the resources, materials, and tasks needed for the job.
- Work order scheduling: The scheduler schedules the work order by allocating dates and times for the tasks. They consider resource availability, equipment downtime, and priority levels.
- Work order execution: Assigned technicians execute the tasks according to the work order. They access task details in SAP PM, perform the work, and log relevant information, such as start and end times, materials used, and observations made during execution.
- Work order completion: Once all tasks are completed, the technician or planner marks the work order as complete. They enter details about time spent, labor hours, and consumed materials, and record any follow-up actions required.
- Work order closure: The planner reviews the work order to ensure all necessary information is captured. They close the work order, update the equipment’s maintenance history, and generate reports for analysis and future planning.
While the functionality is there, the problem with using SAP for WO scheduling is that the software is very clunky and hard to learn. Let’s see why.
Sidenote: We have a webinar that discusses how to build a rolling schedule in SAP with the use of revision codes, how to level work within SAP, and how to use Sockeye to simplify and monitor the weekly schedule. Check it out here!
The challenges of SAP work order management
While SAP is an excellent tool for enterprise resource management, it comes with its own set of challenges that can hinder efficiency — especially when it comes to scheduling.
We’ve seen maintenance teams that would rather stick with Excel, despite the major disadvantages of that approach.
But why does that happen? There are two major problems we want to highlight.
SAP is complex to navigate
The SAP interface isn’t exactly user-friendly, especially for new users. Its complexity often requires extensive training to understand the workflows, and even seasoned users may find the system cumbersome when performing everyday tasks.
Navigating between multiple screens to manage schedules and work orders just isn’t what maintenance teams are looking for — they have enough on their plate without added administrative work.
The system is very rigid
SAP’s scheduling tools are designed with a specific workflow in mind, leaving little room for flexibility. Adjusting your team’s unique processes to fit SAP can feel like trying to fit a square peg into a round hole.
Every step — creating notifications, planning resources, scheduling, execution, and closure — requires very specific inputs. Real-time changes, such as handling emergency repairs or shifting schedules due to unexpected downtime, often require clunky workarounds.
If you want to tweak your workflow or need features that aren’t out-of-the-box, you’re looking at expensive customizations that can run into hundreds of thousands of dollars. That’s a hefty price tag for adaptability.
Here’s the good news. If your company uses SAP, you can integrate it with a work order scheduling app like Sockeye to simplify the process, while still keeping all of your data in a single location.
How Cargill used Sockeye to simplify maintenance scheduling after migrating to a SAP
When Cargill, a global leader in food and agriculture, deployed SAP, they found its scheduling tools rigid and inefficient for their complex maintenance operations — so they needed a new maintenance scheduling solution.
To address this issue, Cargill integrated Sockeye into their workflow. Sockeye’s intuitive scheduling platform simplified their work order management by providing:
- Simplicity: They needed a new, simple-to-use scheduling system to replace their customized spreadsheets.
- Drag-and-drop scheduling: Maintenance planners could easily assign tasks and resources without navigating SAP’s cumbersome interface. Adjustments could be made in seconds, not hours.
- Real-time updates: Changes to schedules and work orders were instantly reflected across the system, ensuring team alignment and reduced downtime.
- Improved visibility: Sockeye’s dashboards offered clear insights into workload distribution, resource availability, and schedule performance.
Rick Baldridge, their Corporate Reliability Excellence Process Leader, explained:
“What I look for is a tool that can enable our business processes without overwhelming people because it’s too cumbersome and complicated. It’s all about simplicity. The simpler it enables the business process, the better. Right out of the box, Sockeye was a great match for our business process. We knew it was a perfect fit.”
The result? A more efficient maintenance process, reduced administrative burden, and better resource utilization.
By integrating Sockeye with SAP, you get the best of both worlds: the robust capabilities of SAP PM combined with Sockeye’s intuitive and flexible scheduling. It’s simple, it saves time, and it will increase your operational efficiency.
Schedule a demo to see how Sockeye can transform your maintenance scheduling and make your team’s job easier.