Scheduled maintenance represents tasks that are assigned (to a technician or a team) and have a deadline. This can include anything from routine inspections to full-scale equipment overhauls.
Scheduled maintenance covers both:
- Recurring tasks: These are maintenance activities that happen on a regular basis, like monthly HVAC filter replacements or annual equipment inspections.
- One-time tasks: These are tasks scheduled for a specific time, such as replacing a part that has a known lifespan or preparing equipment for a seasonal operation.
The main goal of scheduled maintenance is to avoid unexpected equipment failures and help organize your team. By sticking to a schedule, organizations can improve the reliability of their assets, extend equipment lifespan, and reduce unplanned downtime which now costs facilities $129 million a year on average.
What is the difference between planned and scheduled maintenance?
Maintenance first needs to be planned, then scheduled, then executed. As such, planned maintenance is a precursor to scheduled maintenance.
Planning maintenance involves identifying maintenance tasks and developing a strategy for completing them. This includes determining what needs to be done and which resources are required, and getting any necessary approvals.
Scheduling maintenance, on the other hand, focuses the execution of these tasks based on a set timetable. It puts the plan into action by specifying when maintenance activities will occur and who will perform the work.
Key components of scheduled maintenance
Scheduled maintenance relies on several key components to ensure its effectiveness. These elements work together to create a clear, actionable plan:
- Equipment/Asset details: Identify the specific assets requiring maintenance. Include relevant information such as model numbers, serial numbers, and location.
- Maintenance tasks: Clearly define the tasks that need to be performed. This could range from inspections and cleaning to part replacements and calibrations.
- Time intervals: Specify when the tasks should be performed. This might be based on usage (e.g., every 500 operating hours), time (e.g., weekly or monthly), or equipment condition (e.g., vibration sensor alert).
- Assigned resources: Assign the right personnel, tools, and materials for the job. Ensure that technicians have the necessary skills and access to required parts and tools.
By integrating these components, organizations can create a robust preventive maintenance schedule that minimizes downtime and optimizes asset performance.
Types of scheduled maintenance
Scheduled maintenance can be categorized into different types based on how the work is scheduled. This way, organizations can tailor their maintenance strategies to their specific needs and equipment:
- Time-based maintenance: Tasks are performed at regular intervals, such as weekly, monthly, or annually, regardless of equipment condition.
- Usage-based maintenance: Maintenance is scheduled based on usage metrics, such as every 1,000 operating hours or every 10,000 cycles.
- Predictive/condition-based maintenance: Advanced monitoring tools are used to track asset conditions in real time. Maintenance is performed when data indicates potential issues, such as vibration analysis showing wear in a machine part.
- Corrective maintenance: Although often reactive, corrective tasks can also be scheduled for a convenient time after identifying non-critical issues that don’t immediately affect operations.
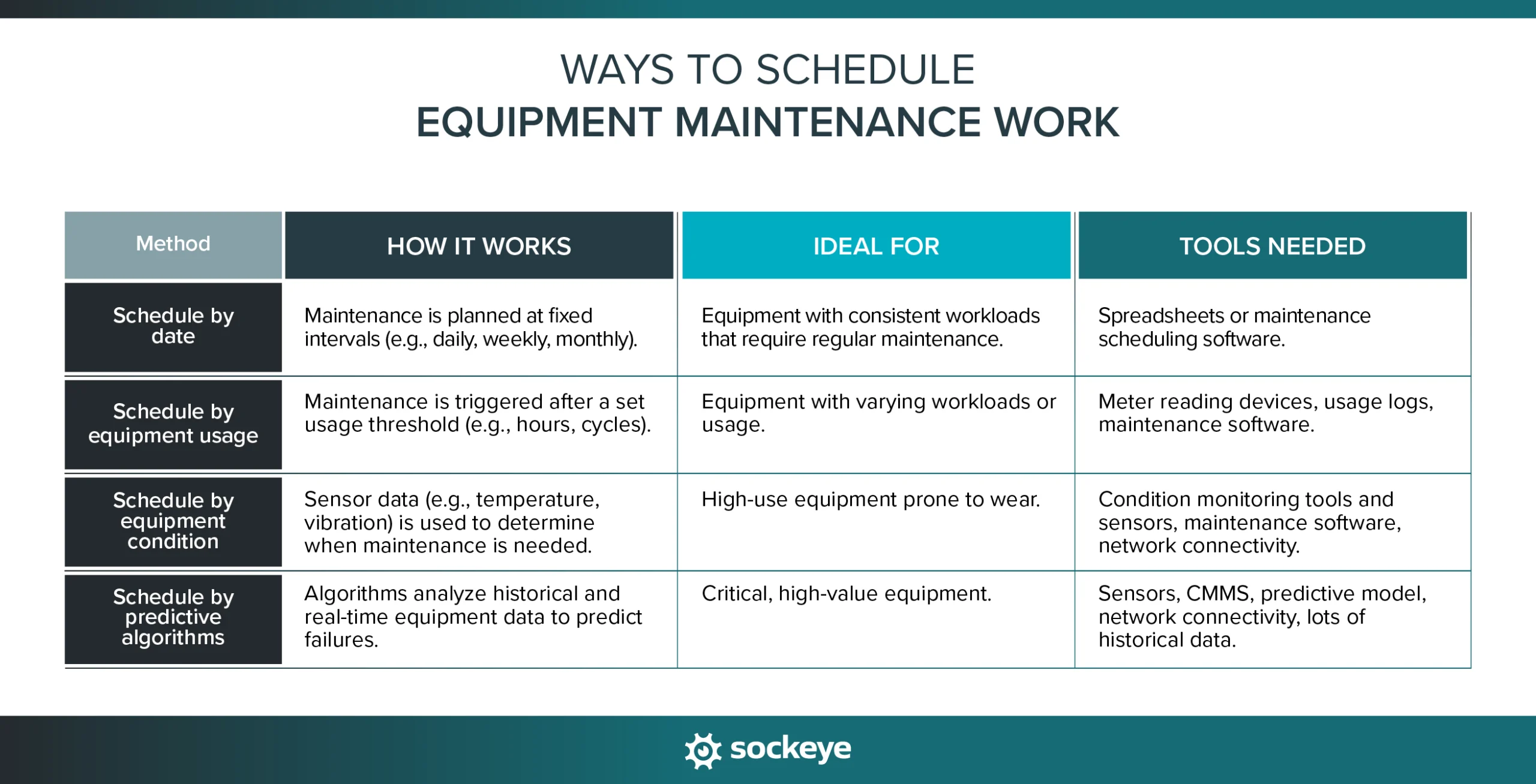
While condition-based maintenance and predictive maintenance are steadily gaining traction, the reality is that proactive teams still predominantly rely on preventive maintenance. If you are in the same boat, it means that you are scheduling most of the work based on usage or time.
Now, the time-based approach can be problematic because work doesn’t always get completed on time.
Imagine you have a weekly inspection scheduled every Thursday. For whatever reason, you have to postpone it 4 days. If you do not update your schedule, next week, you will perform the same inspection twice — once Monday, and then again on Tuesday.
To avoid this issue, instead of following a fixed schedule, maintenance schedulers often use a floating maintenance schedule. So if the inspection was done on Monday, schedulers would just move future inspections from Thursdays to Mondays (of course, if the resource availability allows it).
In the table below, you can see the pros and cons of these basic approaches to scheduled maintenance.
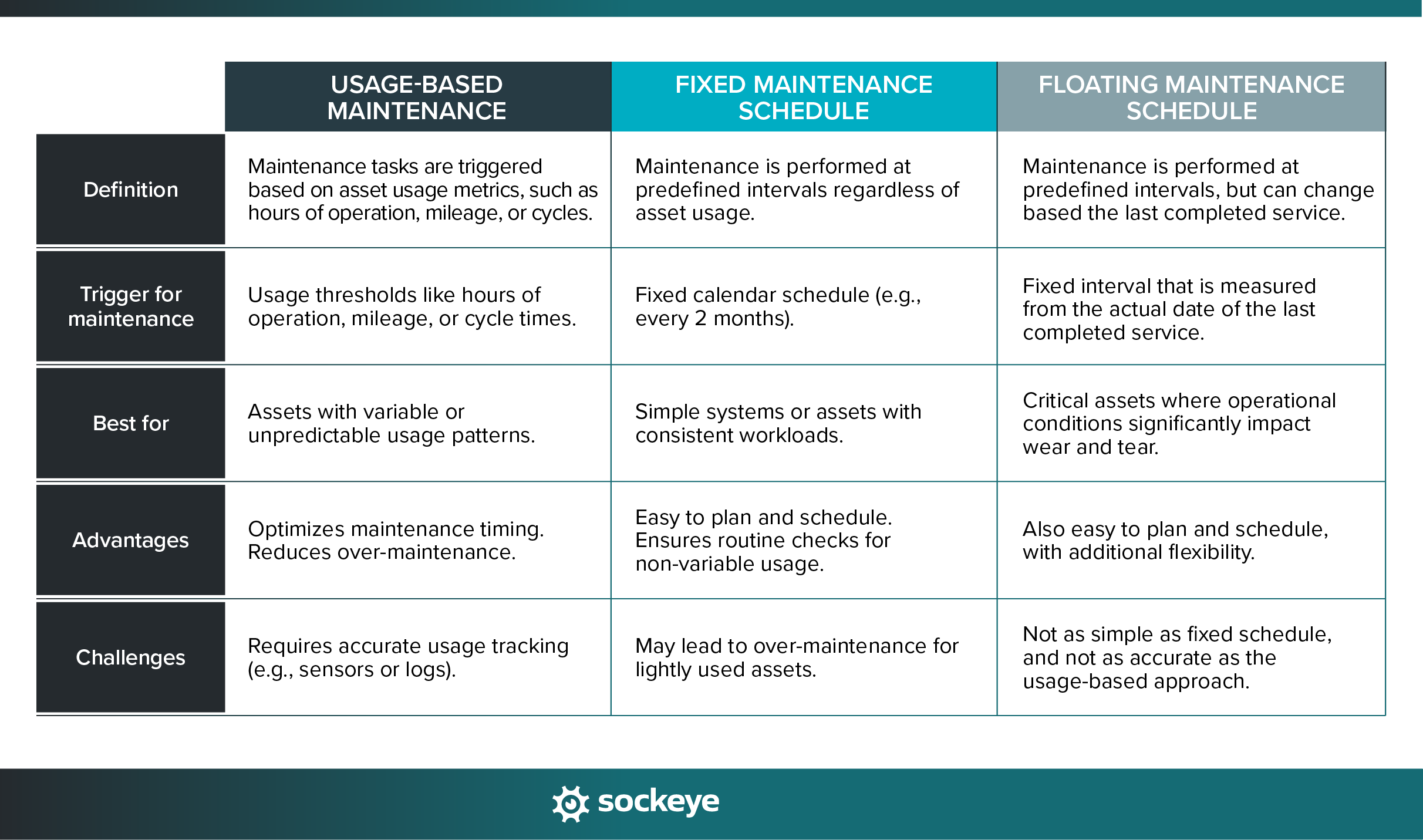
By understanding the differences and use cases for different types of scheduled maintenance, organizations can implement the most appropriate strategy to meet their operational and asset management goals — while staying in line with their maintenance budget.
You have plenty of scheduling options to choose from; what matters is that you stay proactive. To quote Andres Sandes, a Service Manager at KLS Machines:
“If you don’t schedule time for maintenance, your equipment will schedule it for you.”
The role of SMCP in maintenance scheduling
Scheduled Maintenance Critical Percent (SMCP) is a useful tool to help schedulers prioritize recurring scheduled tasks (PMs).
In other words, when you have multiple PMs that are overdue, SMCP helps you identify which one should you prioritize. It calculates the lateness of each PM relative to its designated frequency.
A higher SMCP value indicates a greater urgency, highlighting tasks that should be prioritized.
How to calculate SMCP?
The formula for calculating SMCP is:

Here is a quick calculation example: Imagine you have two PM tasks overdue:
- Task 1: Has PM cycle of 21 days. It is 5 days overdue.
- Task 2: Has PM cycle of 30 days. It is 8 days overdue.
If we pull those numbers through the SMCP formula, we get:
- SMCP for Task 1 = 123.8%
- SMCP for Task 2 = 126.7%
Conclusion? Task 2 is slightly more critical and should be done first.
How to use SMCP?
To effectively use SMCP, you will need to integrate it into your maintenance scheduling process. You can do this by:
- Regularly calculating SMCP for all preventive maintenance (PM) tasks.
- Combining SMCP with other metrics, such as equipment criticality and existing maintenance backlog, to flesh out scheduling prioritization.
- Monitoring SMCP trends to identify inefficiencies, adjust PM cycles, and optimize resource allocation.
- Training staff to understand SMCP and its role in improving maintenance reliability and efficiency.
Scheduled maintenance is simpler with Sockeye
Sockeye is a simple maintenance scheduling app that is most often used as a CMMS bolt-on.
If you are using a CMMS and having trouble navigating through its scheduling functionality, you can integrate your CMMS with Sockeye and use our intuitive interface instead.
Here’s how Sockeye simplifies maintenance scheduling:
- Automated scheduling: Generate maintenance schedules automatically based on your backlog and technician availability. Review and update the schedule with a few clicks.
- Real-time tracking: Monitor task progress and completion in real time to ensure adherence to schedules.
- Resource optimization: Assign tasks efficiently by considering technician availability, and skill sets.
- Insights and reporting: Access detailed reports and analytics to evaluate scheduling performance and identify areas for improvement.
With Sockeye, maintenance managers and schedulers can reduce administrative burdens, improve task visibility, and increase overall operational efficiency.
Want to learn more about Sockeye or have a question about scheduled maintenance? Reach out to our team as we are always glad to help.